Introduction
Looking for a material that combines strength, durability, and design flexibility? Cast steel might be the answer.
Cast steel refers to steel components formed by pouring molten steel into pre-designed molds — a process that enables complex geometries with minimal post-processing. Its combination of strength, ductility, and adaptability makes it essential for demanding industrial applications.
Cast Steel vs. Steel Casting: Clarifying the Terminology
While “cast steel” refers to the final material produced via casting, “steel casting” is the process used to shape molten steel into components. Cast steel is the result of steel casting. Understanding this distinction helps clarify their usage in engineering and procurement contexts.
Key Properties of Cast Steel
- ✅ High tensile and impact strength
- ✅ Excellent ductility and toughness
- ✅ Good weldability and repairability
- ✅ Heat treatable for performance tuning
- ✅ Suitable for dynamic load applications
Common Types of Cast Steel
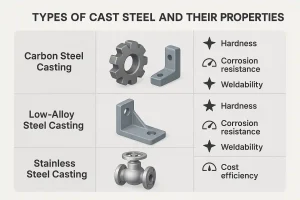
Overview of carbon steel, low-alloy steel, and stainless steel castings with their key properties.
1. Carbon Steel Castings
Steel with 0.2–0.6% carbon content; offers a balance of strength and cost.
- Low Carbon (< 0.25%) – High ductility, general-purpose parts
- Medium Carbon (0.25–0.5%) – Balanced strength and toughness
- High Carbon (> 0.5%) – Higher hardness, wear-resistant parts
Common Grades: ASTM A27 60-30, ASTM A216 WCB
2. Low-Alloy Steel Castings
Alloyed with Cr, Ni, Mo for enhanced properties.
- Improved corrosion and wear resistance
- Higher strength-to-weight ratio
Common Grades: ASTM A217 WC6, WC9
3. Stainless Steel Castings
Containing >10.5% chromium for corrosion resistance.
- Used in pumps, valves, food processing
- Easy to clean, non-reactive surfaces
Common Grades: ASTM A351 CF8, CF8M (equivalent to 304 and 316 stainless steel)
Steel Casting Process
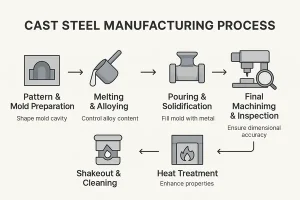
A simplified infographic showing the key steps in the cast steel manufacturing process, from mold preparation to final machining.
Most cast steel components are made using sand casting. Other methods include investment casting and shell molding for finer details.
- Pattern and mold preparation
- Melting and alloying
- Pouring and solidification
- Cleaning and heat treatment
- Final machining and inspection
Advantages of Cast Steel
Feature | Benefit |
---|---|
Design Flexibility | Create complex geometries easily |
Strength | Performs well under dynamic stress |
Weldability | Easier to repair than cast iron |
Customizability | Tailor properties through alloying |
Cost-Effectiveness | Competitive for medium-large parts |
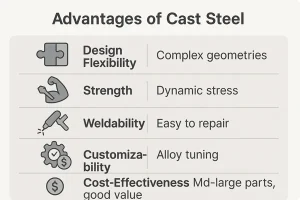
Overview of cast steel advantages for industrial applications
Typical Applications
- Automotive: Housings, brackets, suspension arms
- Energy & Oil: Valve bodies, turbine casings
- Construction: Structural joints, machine bases
- Mining & Rail: Bogie frames, track wear parts
- General Machinery: Gearboxes, pump housings
Choosing the Right Grade
When selecting cast steel, consider:
- ✅ Load-bearing requirements
- ✅ Corrosion or abrasion exposure
- ✅ Weldability or machinability
- ✅ Operating temperature
- ✅ Budget and lifecycle costs
Consult your foundry or materials engineer for critical applications.
When to Choose Cast Steel?
Use cast steel when:
- You require both strength and complex shapes
- Parts will be subject to fatigue or impact
- You need field-repairable parts (via welding)
- Durability matters more than initial cost
Conclusion
Cast steel bridges the gap between forged durability and casting flexibility. From pressure valves to structural components, it remains a reliable, cost-effective solution in industrial manufacturing.
Need Expert Help?
Looking for high-quality cast steel parts or custom steel casting solutions?
👉 Contact Us to get engineering support and cost-effective production.