Low Tooling Investment and Fast Turnaround: A Strategic Advantage
For large metal components, tooling costs and lead times are often decisive factors in the feasibility of a project. Sand casting offers a clear advantage on both fronts—particularly when flexibility, customization, and shorter production cycles are critical.
Unlike die casting or investment casting, which require high-precision steel molds that can cost $20,000 or more, sand casting uses temporary molds made from sand and binders. These molds are far less expensive to produce and can typically be prepared in a matter of days. For example, casting a 1-meter gearbox housing in sand may require a tooling investment of just $2,000—nearly one-tenth the cost of a comparable metal mold.
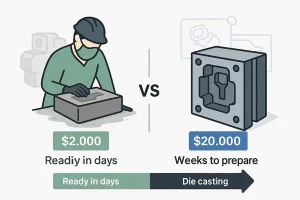
Side-by-side visual showing cost-efficiency of sand casting vs speed advantage of die casting
Speed is only part of the equation. Sand molds can be easily adjusted or rebuilt to accommodate design changes, making the process ideal for engineering trials, reverse engineering, and made-to-order parts. In industries like mining, marine, and energy—where large components often require multiple revisions or on-demand replacement—this level of flexibility reduces both project risk and capital waste.
A permanent mold may lock your design decisions early. A sand mold gives you the freedom to evolve.
Benefits at a Glance:
-
Lower upfront investment for mold development
-
Rapid turnaround from CAD to first pour
-
Design agility with low-cost revisions or rebuilds
If your production plan includes medium-size batches, pilot runs, or late-stage design iterations, sand casting provides the tooling efficiency and response speed modern industrial workflows demand.
Design Freedom: Supporting Complex, Large-Scale Geometries
One of the most valuable yet often underestimated advantages of sand casting is its exceptional design flexibility—particularly when it comes to large, geometrically complex components. Unlike permanent metal molds, which impose strict limitations on shape, draft angle, and parting lines, sand molds are formed around custom patterns and can be tailored to support virtually any geometry.
Sand casting accommodates internal features such as hollow sections, ribs, bosses, and cross-drilled channels using removable sand cores.
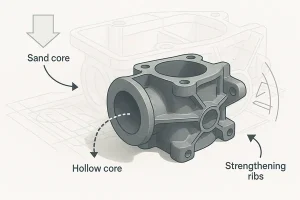
Sand casting enables intricate features like hollow sections and structural ribs in large components
These features can be integrated into a single pour, eliminating the need for welding, assembly, or multiple casting steps. Engineers can optimize structural performance, reduce weight, and simplify downstream machining—all without compromising manufacturability.
This capability is especially important for large components in demanding applications, such as:
-
- Pump housings with integrated flow paths
-
- Engine blocks with internal cooling galleries
-
- Wind turbine hubs with deep multi-axis cavities
-
- Heavy machinery frames with embedded reinforcement ribs
Because sand molds are disposable, design changes are easy and inexpensive to implement. Whether it’s repositioning a bolt hole, altering wall thickness, or adapting a flange, engineers can make adjustments without discarding costly tooling. This flexibility allows for late-stage design refinement, prototyping, or rapid iteration during development cycles.
Complex geometry shouldn’t be a constraint—it should be a design opportunity.
In industries where size and performance matter just as much as precision, sand casting enables engineers to fully realize their design intent. It removes the constraints imposed by rigid tooling and supports innovation at scale.
Compatible with High-Temperature Alloys Like Steel and Ductile Iron
Sand casting excels where many other methods fail: handling high-melting-point metals such as carbon steel, alloy steel, and ductile iron. These materials are essential for heavy-duty applications that demand strength, heat resistance, and long service life—but they pose serious challenges for casting processes that rely on permanent molds.
Die casting, for example, is optimized for low-melting alloys like aluminum, magnesium, or zinc. Its steel molds simply cannot withstand the extreme temperatures—often exceeding 1500°C (2730°F)—required to pour molten steel or iron.
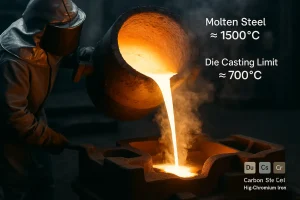
Molten metal being poured into a sand mold, suitable for high-temperature alloys like ductile iron and steel
Even with cooling systems, the thermal fatigue on the tooling makes die casting technically and economically impractical for these metals.
Sand casting avoids this problem entirely. Using heat-resistant silica or chromite sand, the molds are fully disposable and unaffected by molten metal temperatures. This makes the process ideal for casting ferrous alloys, including:
-
- Ductile iron for gearbox housings and suspension arms
-
- Low-alloy steel for wind turbine hubs and drivetrain frames
-
- High-chromium irons for wear-resistant liners in mining and crushing equipment
Because of this compatibility, sand casting is the default choice for structural and pressure-bearing components in industries like power generation, off-highway machinery, and marine engineering.
You don’t choose sand casting just for geometry—you choose it when the metal itself demands it.
When your project calls for robust performance in high-stress or high-heat conditions, sand casting delivers the material flexibility other methods simply can’t support.
Overcoming Defects: How Modern Sand Casting Ensures Quality
Sand casting has historically been associated with surface roughness, dimensional variability, and internal defects. But in modern foundries, those issues are no longer inherent to the process—they’re engineering problems with known, controlled solutions.
Today’s casting workflows incorporate CAE-based solidification simulation, automated molding systems, and non-destructive testing (NDT) to ensure part quality from pattern to final inspection. The result: sand castings that consistently meet demanding industrial specifications.
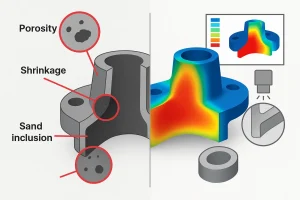
Side-by-side visual showing traditional trial-and-error sand casting versus modern simulation for better accuracy
Common Defects and Modern Solutions:
-
- Porosity & Shrinkage
Eliminated using 3D solidification modeling, riser optimization, and controlled cooling curves
- Porosity & Shrinkage
-
- Sand Inclusion
Prevented through proper gating design, filtration systems, and mold cleaning procedures
- Sand Inclusion
-
- Distortion or Warping
Reduced by uniform mold compaction and consistent binder application
- Distortion or Warping
By simulating heat flow and metal solidification before the first pour, engineers can identify risk areas like hot spots and ensure optimal mold geometry and venting. This proactive approach drastically reduces defect rates—especially in large, high-mass components.
Application Example:
In a recent gearbox housing project for mining equipment, simulation revealed a risk of shrinkage at bolt flange intersections. Engineers repositioned risers and adjusted cooling paths. The result: first-shot success, verified by ultrasonic inspection (UT), with no rework required.
Conclusion:
Modern sand casting is quality-capable and process-controlled. With digital tooling, advanced diagnostics, and rigorous inspection—ultrasonic, radiographic, and dye penetrant—it delivers consistent performance for critical parts in industries like power generation, construction, and transportation.
When precision meets process discipline, sand casting becomes a trusted solution—not a compromise.
When to Choose Sand Casting Over Other Methods
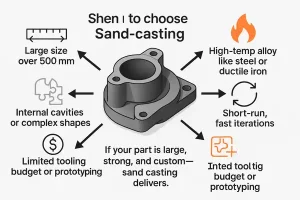
Visual guide to selecting sand casting for large, custom, high-temperature components.
With a wide range of casting technologies available—die casting, investment casting, permanent mold—it’s important to know when sand casting is the best fit. The choice depends on several key factors: part size, geometry, alloy, quantity, and design flexibility.
Sand casting is your best option when:
-
The part is large (typically over 10 kg or 500 mm in size)
-
The material is a high-temperature alloy like steel or ductile iron
-
The design includes complex internal features, ribs, or cavities
-
You need short-run production, rapid prototyping, or aftermarket replacements
-
Late-stage design changes or customization are expected
In contrast, die casting is ideal for small-to-medium aluminum or zinc components produced at very high volumes with tight dimensional tolerance. Investment casting is best for small, intricate parts that require excellent surface finish—but comes with higher per-unit cost and longer tooling time.
Sand casting isn’t just a fallback—it’s a strategic process for size, complexity, and adaptability.
Final Note:
If your project demands structural strength, engineering flexibility, and economic efficiency—without committing to high-volume tooling—sand casting is the solution that aligns with real-world industrial needs.
Explore our sand casting capabilities or get in touch for a quote. We’ll help you assess feasibility and optimize for performance.