- Home
- Services
- Steel Casting
Steel Casting
Durable and high-strength steel castings for demanding applications. Suitable for construction, mining, and heavy industrial components. ISO 9001 certified, ±0.05mm tolerance, heat-treated if required.
Why Choose Our Steel Casting Services
Over two decades of expertise in producing high-strength steel castings — engineered for performance in the world’s toughest environments.
Strength & Durability
Our steel castings are built for impact resistance, load-bearing applications, and long-term service life — ideal for construction, mining, and heavy equipment. .
Versatile Material Options
We offer a wide range of steel grades, including carbon steel, alloy steel, and stainless steel — customized for your mechanical and corrosion requirements. .
Flexible Prototyping & Production
From low-volume prototypes to high-volume production, we support rapid development with lead times as short as 10 days. .
Full-Process Quality Control
Each casting undergoes dimensional checks, non-destructive testing (NDT), and material certification to ensure reliability under critical conditions. .
Our Steel Casting Process
From mold design to final inspection, our steel casting process ensures structural integrity and performance under the most demanding conditions.
1. Mold Engineering
Custom molds are created using CAD and simulation tools to ensure proper solidification and casting precision for steel parts. .
2. Steel Melting & Pouring
We melt steel in induction or arc furnaces and pour into sand or investment molds — ensuring material consistency and metallurgical quality. .
3. Heat Treatment & Machining
Parts are heat-treated to improve strength, toughness, or wear resistance, followed by CNC machining for precise dimensional control. .
4. Testing & Surface Finishing
Each casting undergoes NDT (such as UT/RT/MT), surface cleaning, and final inspection to meet functional and cosmetic requirements. .
Our Steel Casting Capabilities
We provide custom steel casting services to meet demanding industrial applications — from wear-resistant components to large structural parts.
Specification | Details |
---|---|
Casting Weight Range | 1 kg – 500 kg |
Typical Materials | Carbon Steel, Alloy Steel, Stainless Steel |
Annual Capacity | 100,000+ parts |
Machining Tolerance | ±0.1 mm (after heat treatment) |
Tooling Lead Time | 20–35 days |
Our Steel Casting Projects
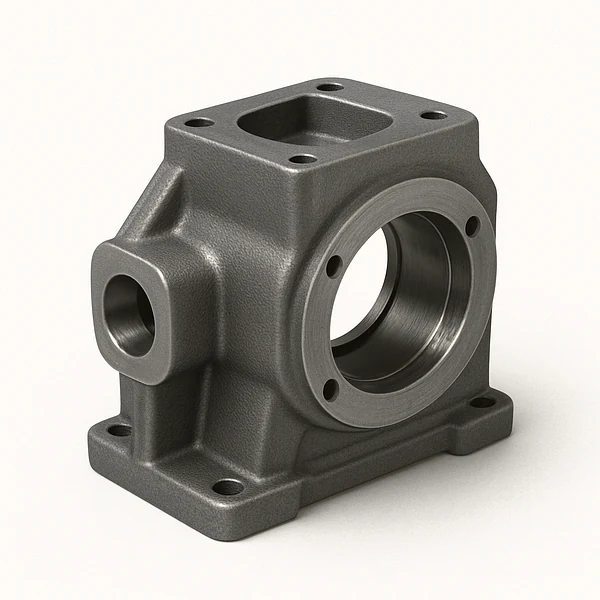
Heavy-Duty Gearbox Housing
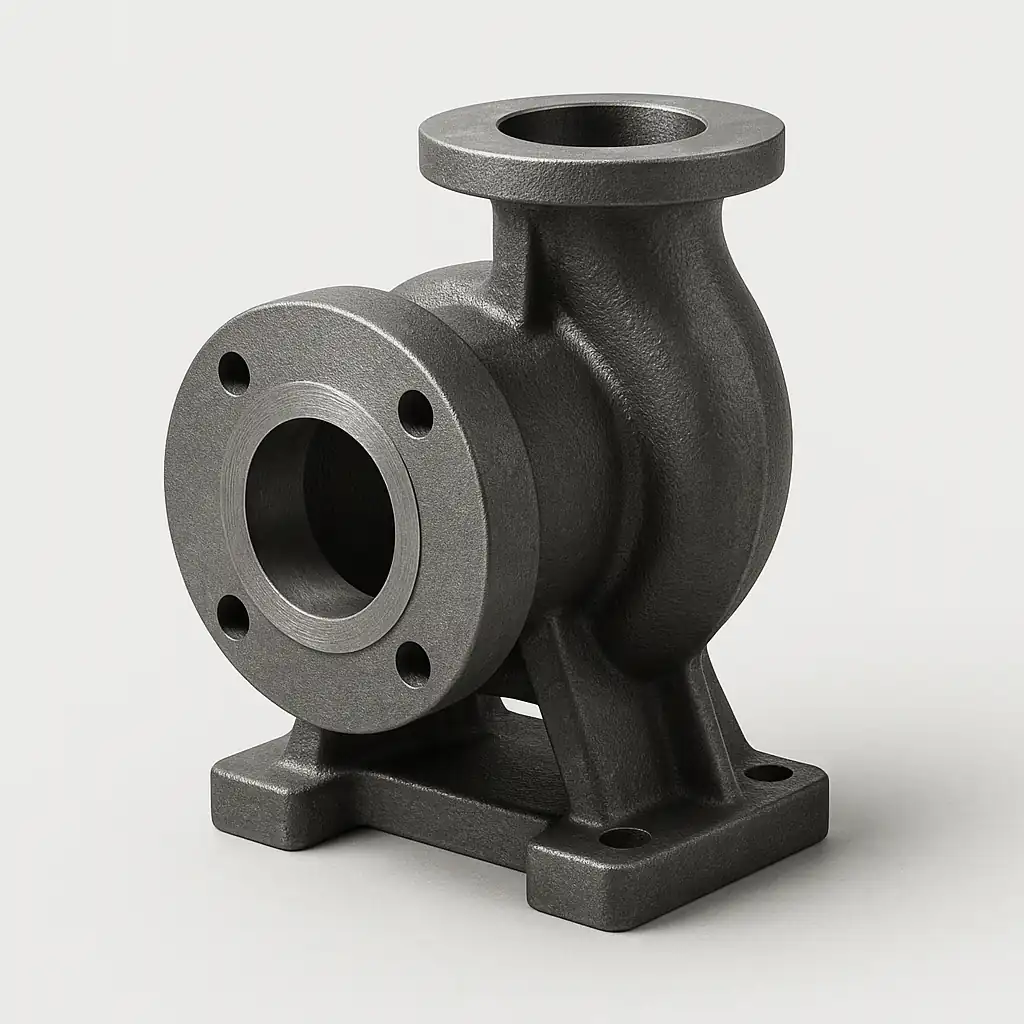
Pump Body (Steel Casting)
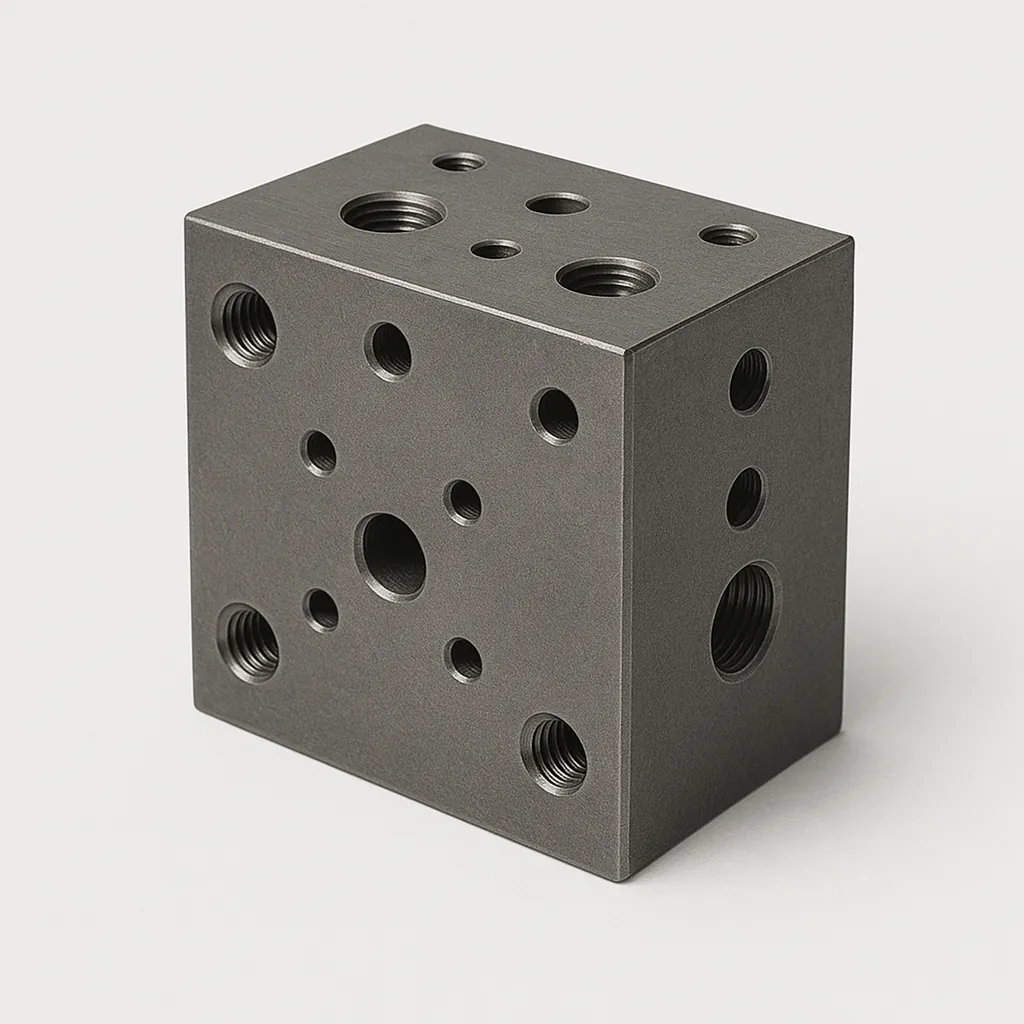
Hydraulic Valve Block
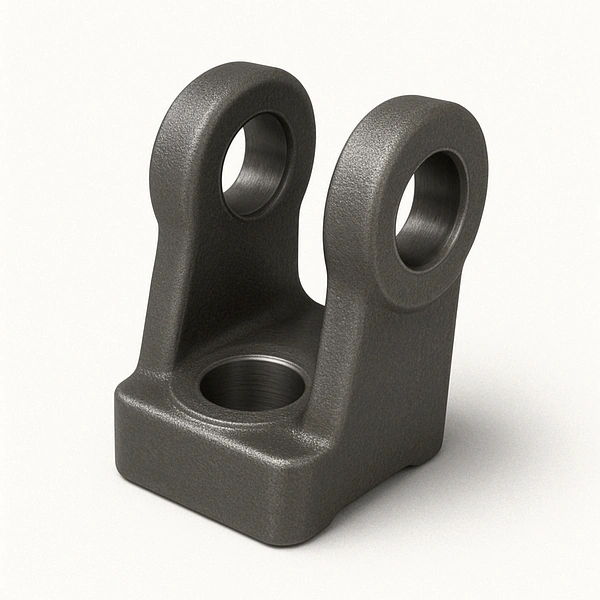
Excavator Arm Joint (Yoke)
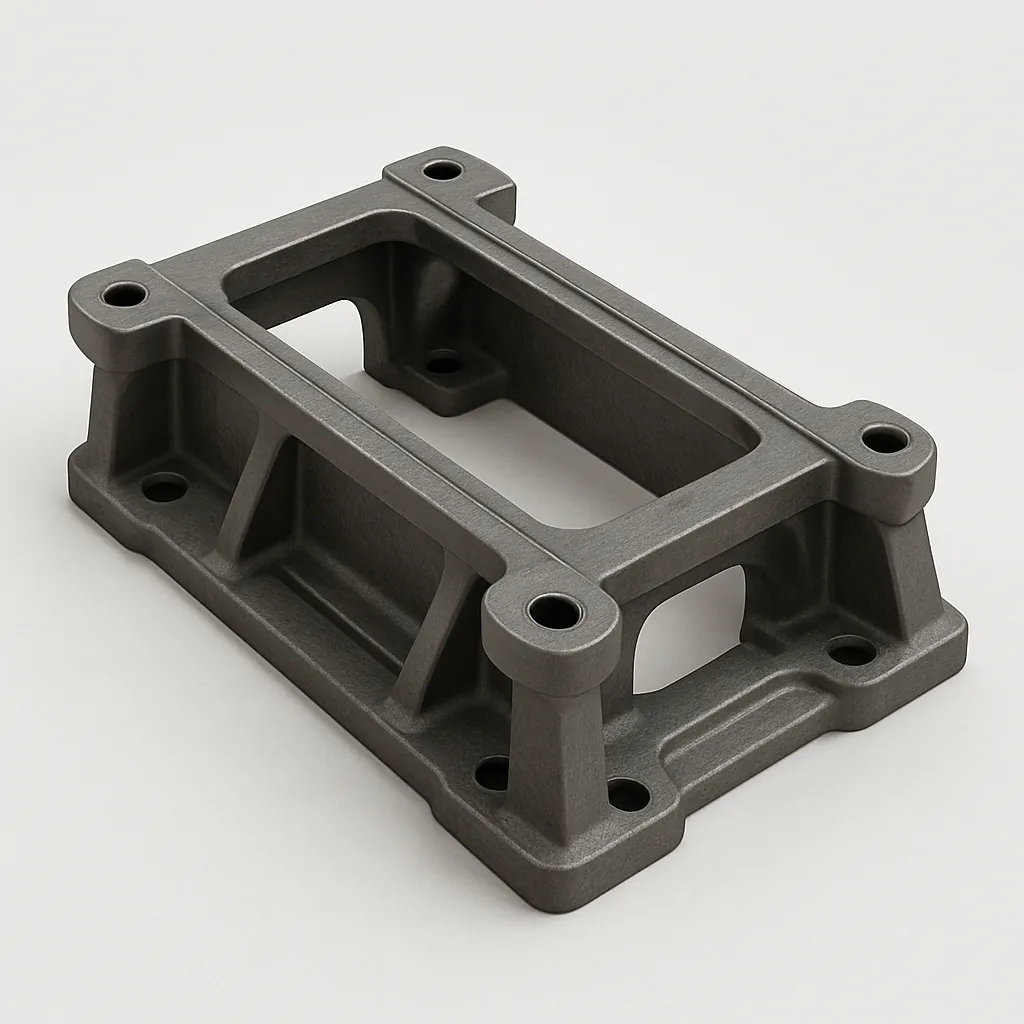
Turbine Base Frame
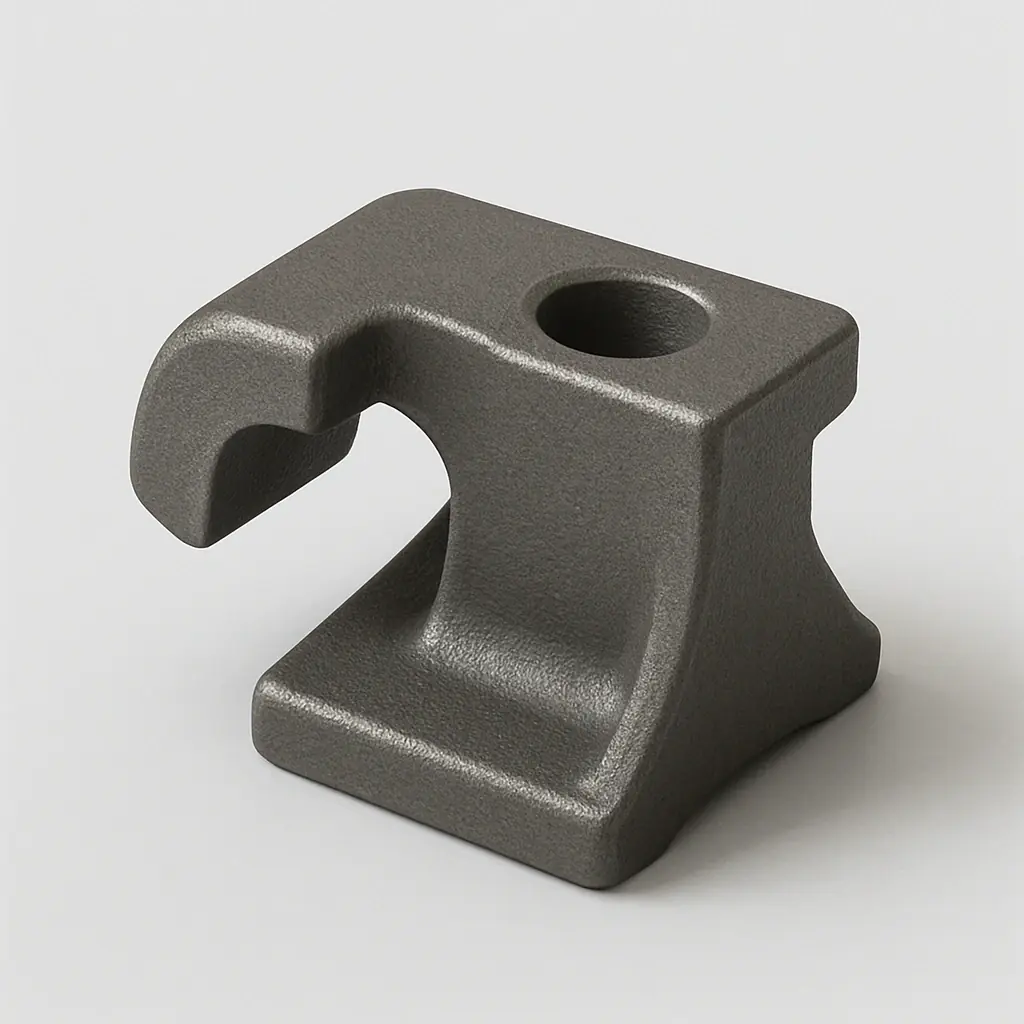
Rail Clamp Component
FAQ – Frequently Asked Questions
- High mechanical strength
- Excellent toughness and impact resistance
- Customizable for complex shapes and heavy loads
- Suitable for high-temperature and high-pressure environments
- Sand Casting
- Investment Casting
- Shell Mold Casting
- Lost Foam Casting
- Advanced mold and gating design
- Non-destructive testing (NDT) such as UT, RT, or MT
- Material certification and inspection reports
- Dimensional checks after machining