- Home
- Services
- Cast Iron
Cast Iron
Durable and high-strength steel castings for demanding applications. Suitable for construction, mining, and heavy industrial components. ISO 9001 certified, ±0.05mm tolerance, heat-treated if required.
Why Choose Our Cast Iron Services
Over 20 years of experience in producing durable and precision cast iron components — trusted by industries worldwide.
High Strength & Wear Resistance
Our cast iron parts are designed for load-bearing, vibration-damping, and wear-resistant applications — ideal for construction and heavy machinery. .
Material Flexibility
We offer both gray iron and ductile iron grades (HT200, QT450, QT500) to meet varied mechanical and performance needs. .
Short Lead Times
Standard lead times from 15 to 30 days. We support small batch prototyping and fast production turnaround. .
Strict Quality Assurance
All parts undergo dimensional checks, NDT (UT/RT/MT), and material testing to ensure structural integrity and consistency. .
Our Cast Iron Casting Process
From mold design to final inspection, our cast iron process ensures durability, dimensional accuracy, and cost-efficiency across all applications.
1. Mold Engineering
Custom sand or resin molds are designed using CAD and simulation tools to optimize solidification and reduce internal defects in iron castings. .
2. Iron Melting & Pouring
We melt gray or ductile iron in cupola or induction furnaces and pour into preheated molds — ensuring metallurgical stability and clean castings. .
3. Cooling & Cleaning
After controlled cooling, castings undergo shakeout, sand removal, and rough cleaning to prepare for further processing. .
4. Inspection & Finishing
Each part is inspected for dimensional accuracy and defects. Optional machining or surface treatment is applied based on final use. .
Our Iron Casting Capabilities
We provide custom iron casting services to support a wide range of industrial needs — from durable gray iron to high-strength ductile iron components.
Specification | Details |
---|---|
Casting Weight Range | 0.5 kg – 800 kg |
Typical Materials | Gray Iron (HT200), Ductile Iron (QT450, QT500) |
Annual Capacity | 150,000+ parts |
Machining Tolerance | ±0.2 mm (after stress relief or annealing) |
Tooling Lead Time | 15–30 days |
Our Iron Casting Projects
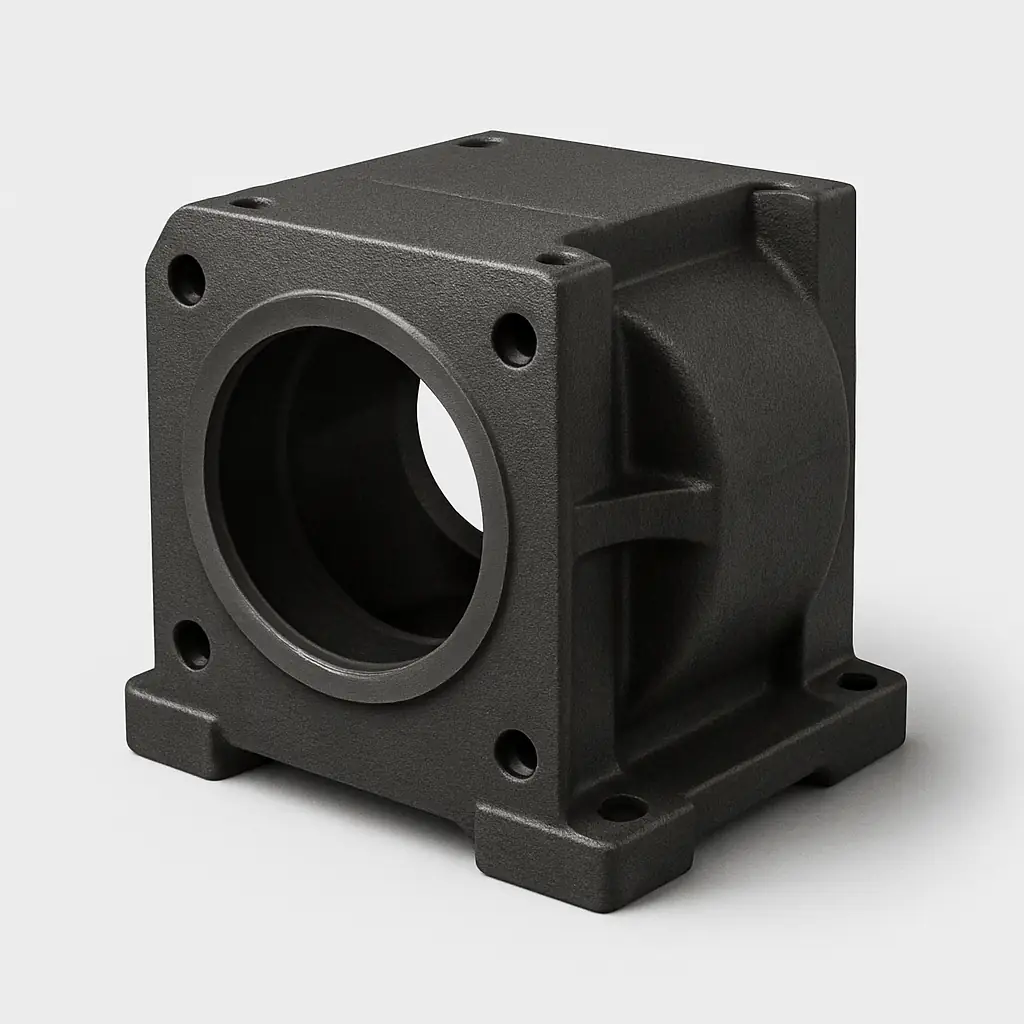
Cast Iron Gearbox Housing
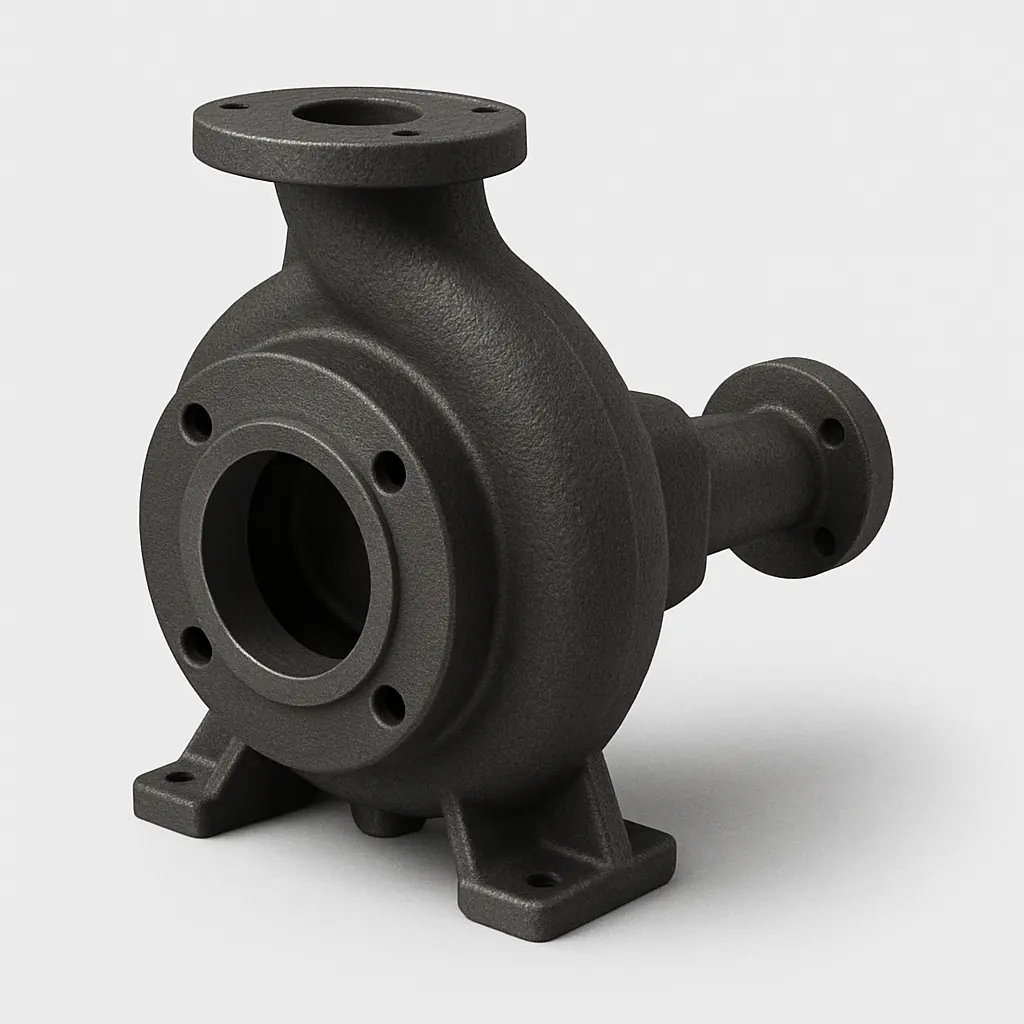
Cast Iron Pump Casing
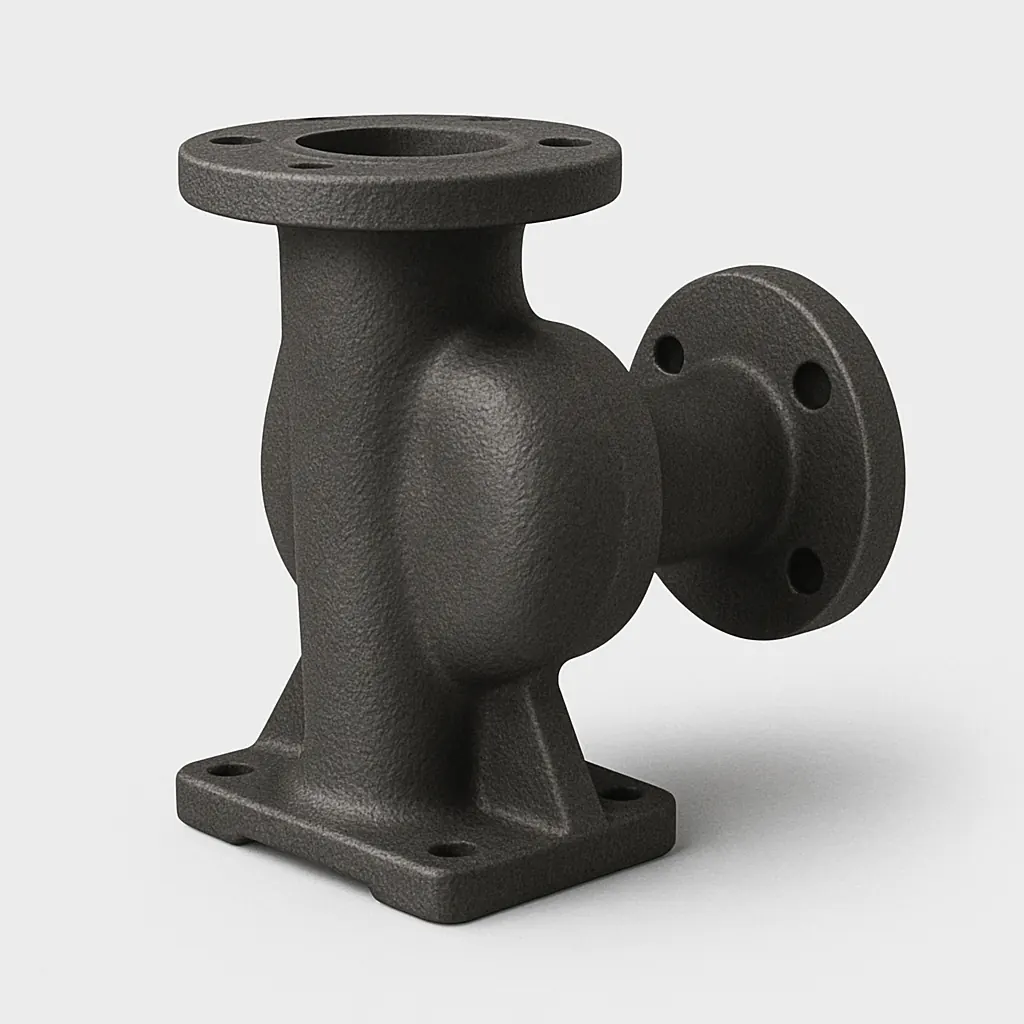
Cast Iron Valve Body
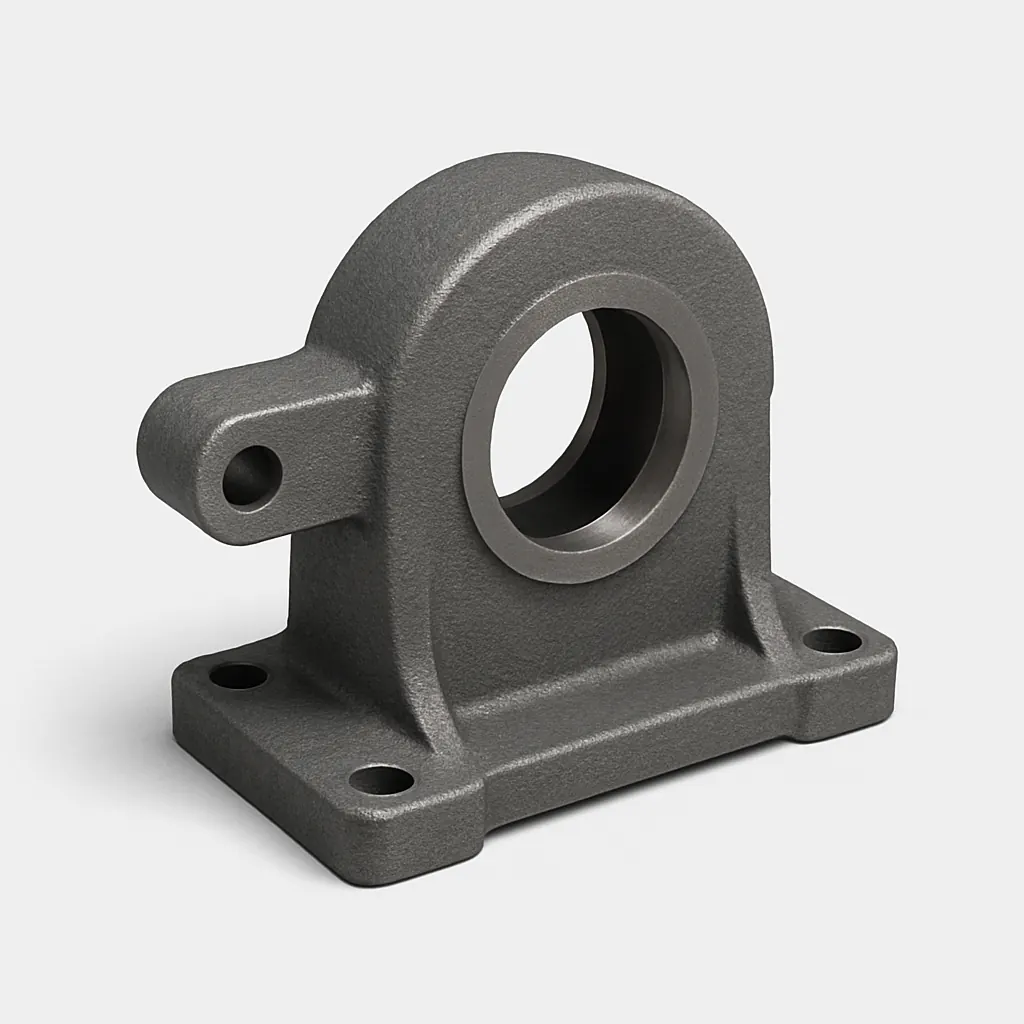
Excavator Yoke (Ductile Iron)
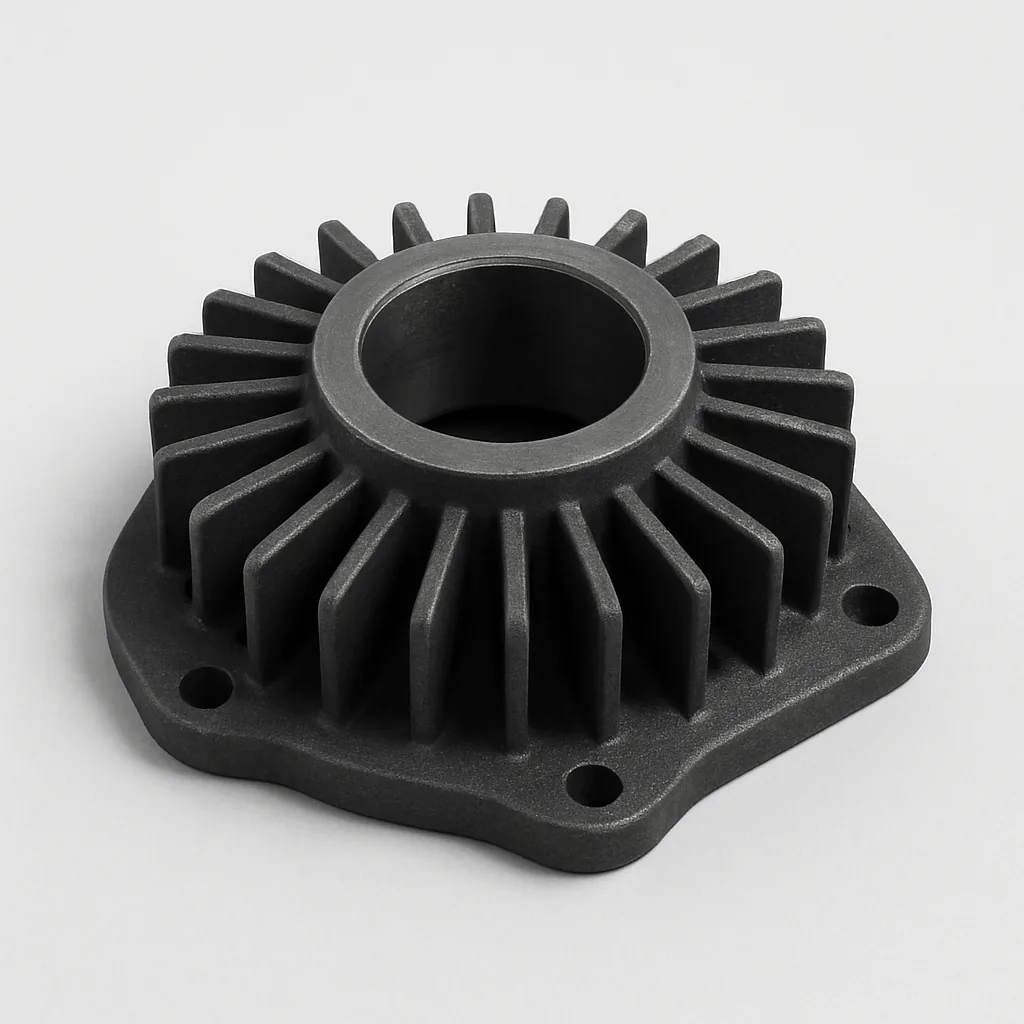
Turbine Support Base(Cast Iron)
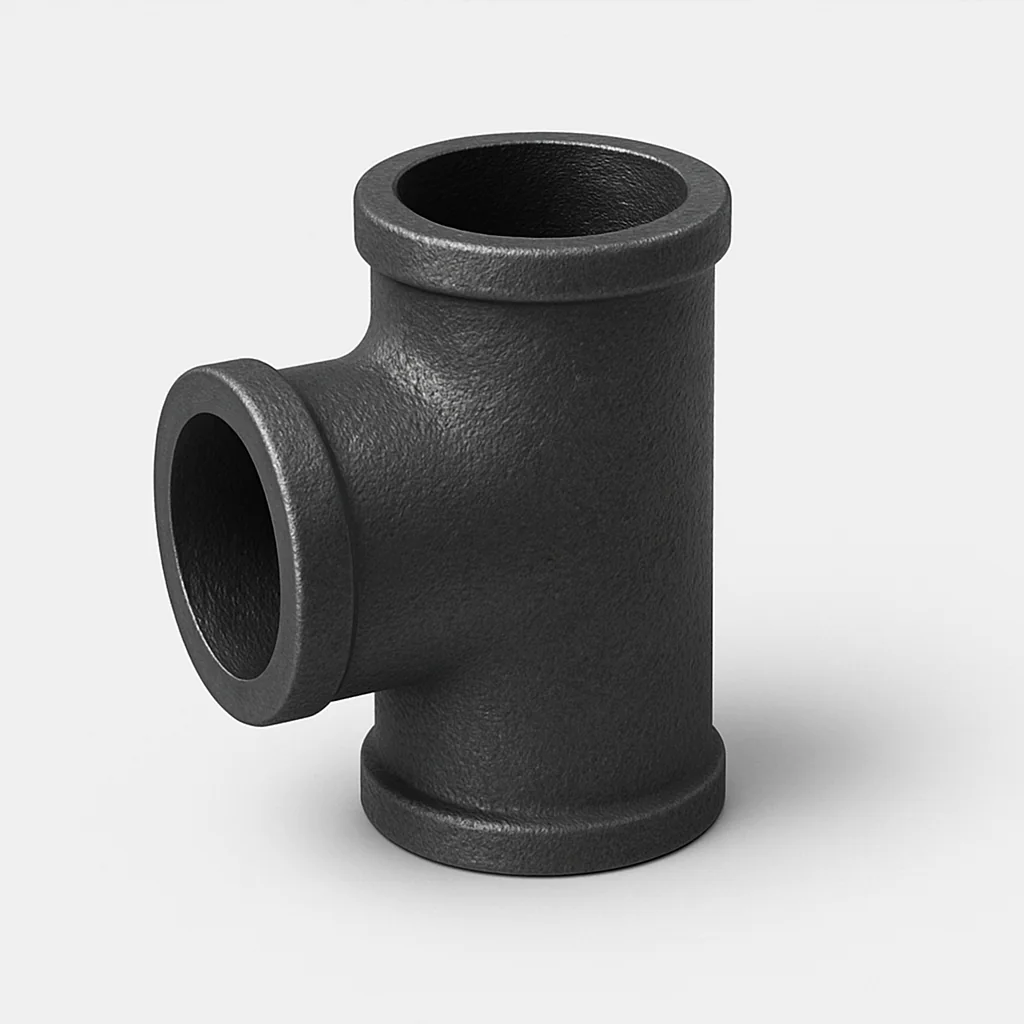
Cast Iron Pipe Tee
FAQ – Frequently Asked Questions about Iron Casting
- Excellent vibration damping and wear resistance
- Cost-effective for large volume production
- Good machinability and thermal conductivity
- Suitable for automotive, pump, and industrial components
- Green Sand Casting
- Resin Sand Casting
- Shell Mold Casting
- CAD-based mold design and simulation
- Metallurgical testing and chemical analysis
- Dimensional inspections and NDT (UT/MT) if required
- Final surface and machining quality checks