- Home
- Services
- Aluminum Casting
Aluminum Casting
Durable and high-strength steel castings for demanding applications. Suitable for construction, mining, and heavy industrial components. ISO 9001 certified, ±0.05mm tolerance, heat-treated if required.
Why Choose Our Aluminum Casting Services
An ISO 9001-certified aluminum casting foundry with over 25 years of experience, providing reliable, high-precision custom solutions worldwide.
Precision & Consistency
We ensure every casting meets tight tolerance and smooth surface finish requirements through precision CNC machining and strict process control. .
Wide Range of Aluminum Alloys
Choose from a wide selection of alloys, including A356, ADC12, 6061, and more — tailored for automotive, aerospace, and industrial uses. .
Rapid Prototyping & On-Time Delivery
Quick response for new projects: samples in 7 days, mass production in 15–30 days — always on schedule. .
Rigorous Quality Control System
ISO 9001-certified system, full-process inspection, and testing with calipers, spectrometers, and 3D metrology equipment. .
Our Aluminum Casting Process
From mold design to final finishing, our aluminum casting process ensures precision and consistency at every stage.
1.Mold Design
Custom molds are developed using CAD software to ensure accurate geometry and casting feasibility. .
2.Aluminum Casting
We melt and pour high-quality aluminum alloys using gravity or die casting methods for optimal integrity. .
3.CNC Machining
Tight tolerances and smooth finishes are achieved through advanced CNC machining processes. .
4.Finishing & Inspection
Parts undergo surface treatment, full inspection, and quality verification per ISO standards. .
Our Aluminum Casting Capabilities
We provide aluminum casting services tailored to your specific requirements — from small precision parts to large industrial components
Specification | Details |
---|---|
Casting Weight Range | 0.05 kg – 30 kg |
Typical Alloys | ADC12, A356, ZL101 |
Annual Capacity | 500,000+ parts |
Machining Tolerance | ±0.05 mm |
Tooling Lead Time | 15–25 days |
Our Aluminum Casting Projects
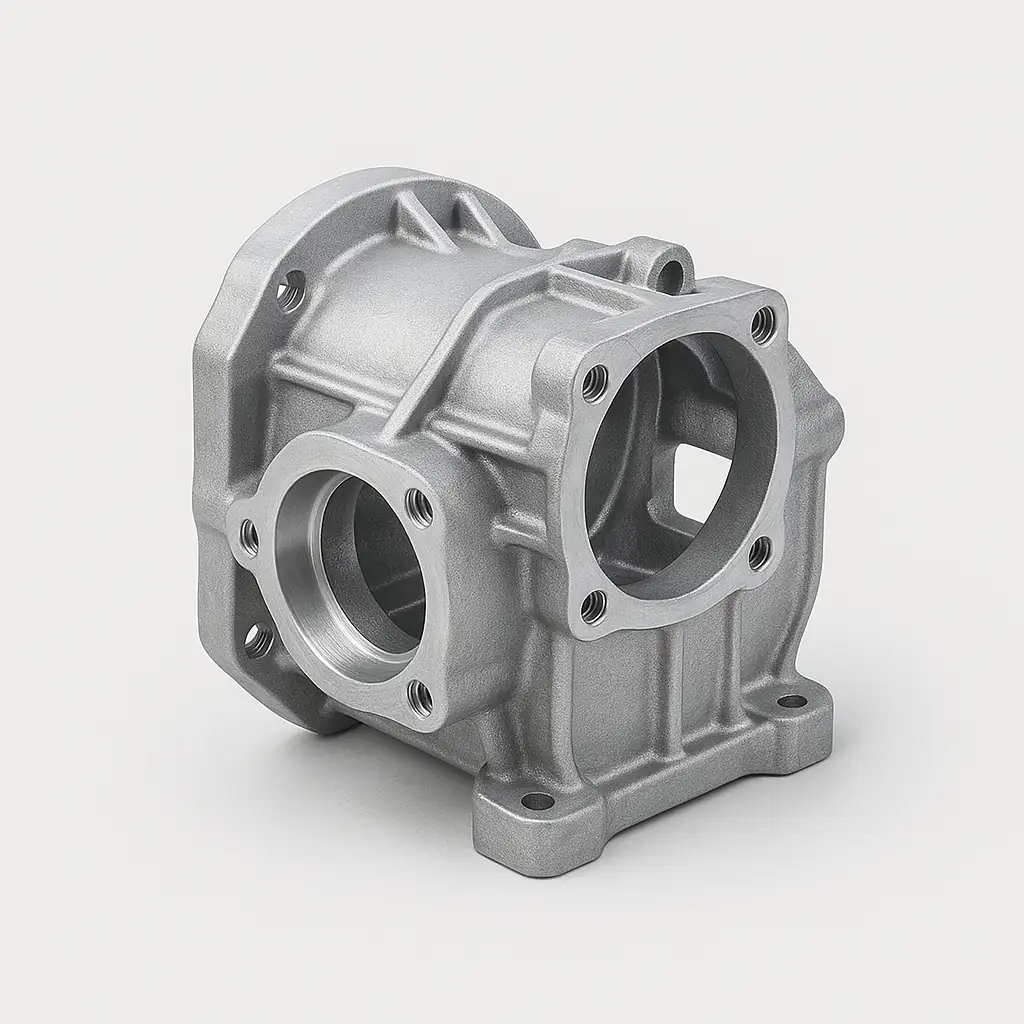
Die Cast Gearbox Shell
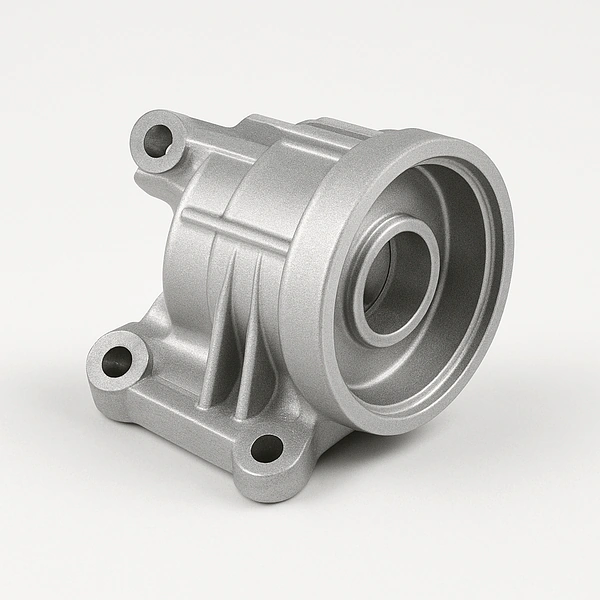
Aluminum Pump Housing
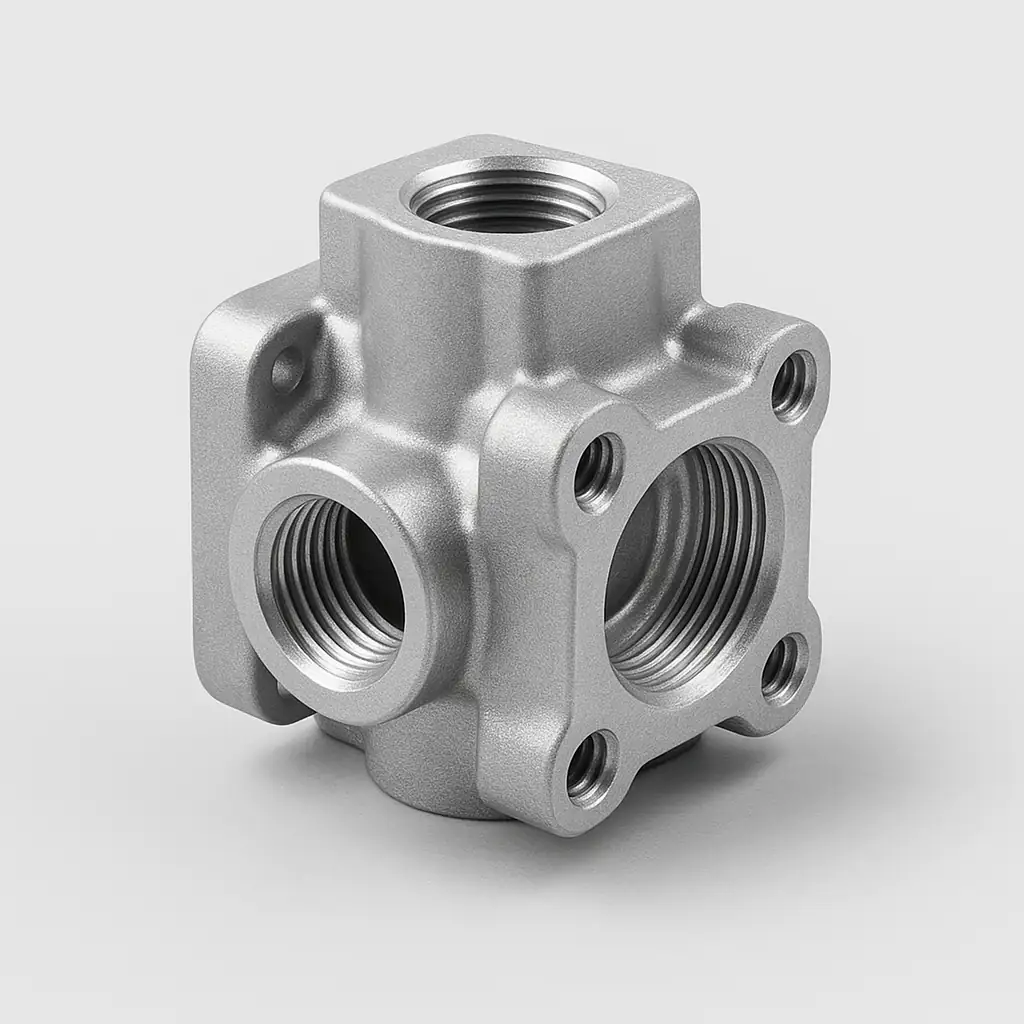
Die Cast Valve Housing
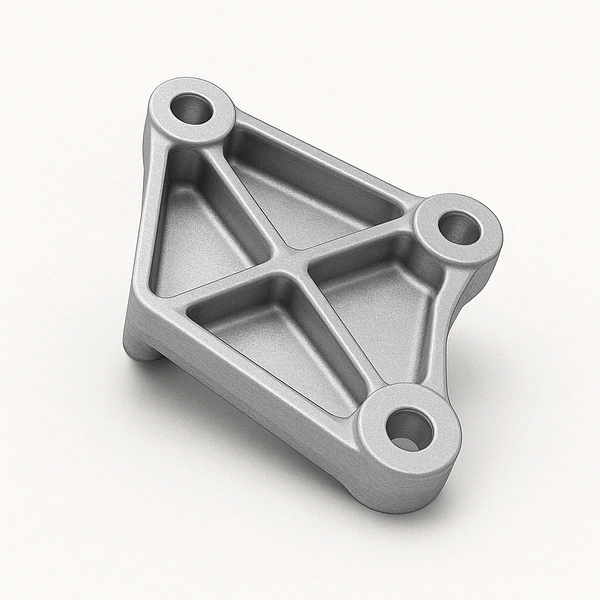
Aluminum Engine Bracket
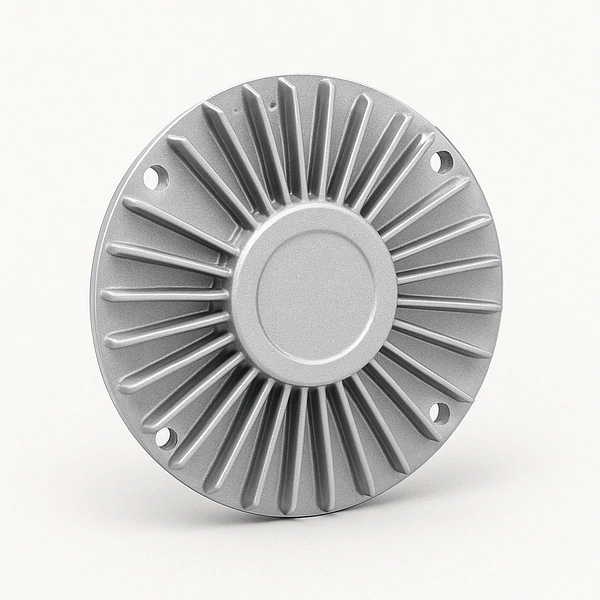
Die Cast Fan Cover
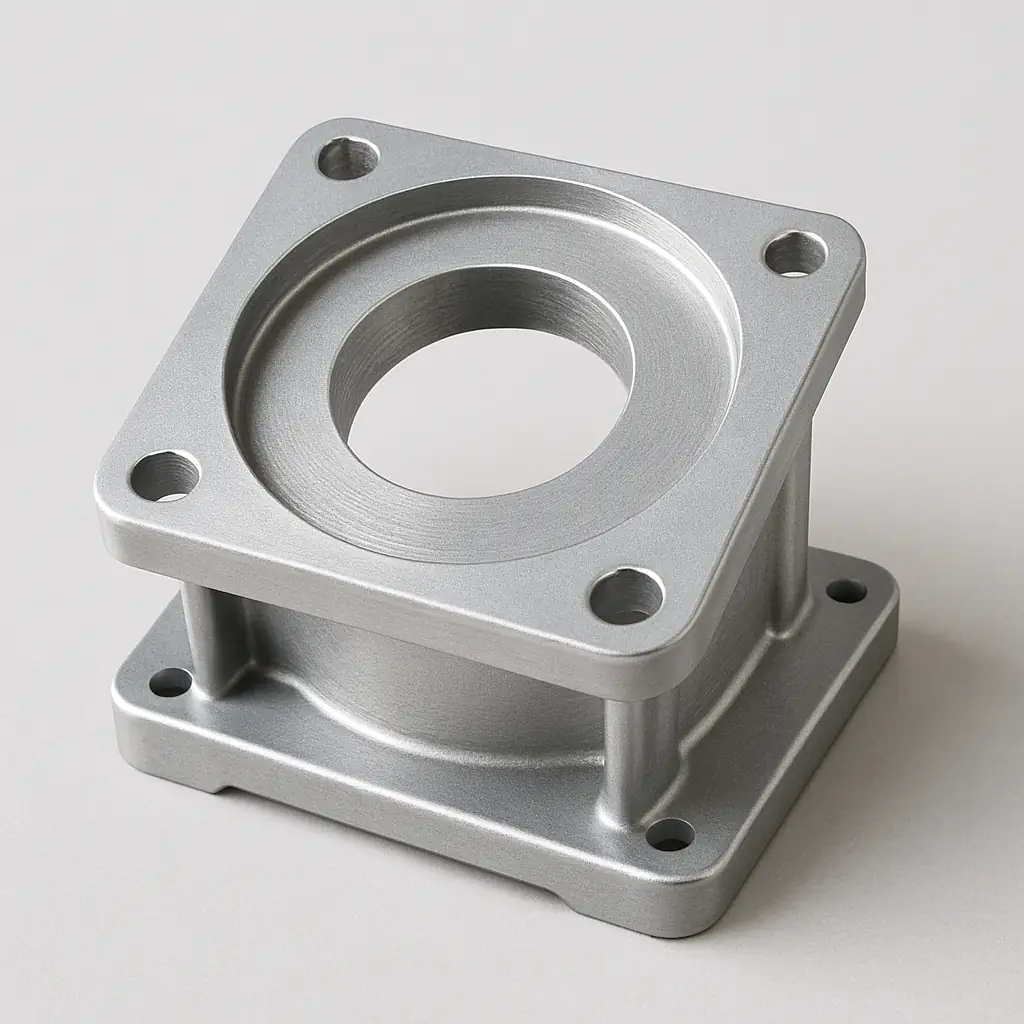
Aluminum Motor Base
FAQ – Frequently Asked Questions
- Lightweight
- Corrosion-resistant
- Excellent for complex shapes
- Good thermal conductivity and dimensional stability
- Die Casting
- Sand Casting
- Permanent Mold Casting
- Investment Casting (Lost Wax)
- Centrifugal Casting
- Anodizing – for corrosion resistance and appearance
- Powder Coating – for durable, decorative finishes
- Painting or Polishing – based on application requirements
- Optimizing mold design
- Using vacuum or pressure-assisted casting
- Employing non-destructive testing (NDT)
- Applying post-treatments such as impregnation