회색 다리미와 연성 다리미: 주요 차이점 및 선택 방법
주철 부품을 소싱할 때 엔지니어와 구매자가 가장 먼저 하는 질문은 다음과 같습니다:
회색 철 또는 연성 철을 사용해야 하나요?
언뜻 보기에는 예산이나 필요한 강도에 따라 답이 달라지는 것처럼 보일 수 있습니다. 하지만 실제로는 부품의 하중 유형, 진동 환경, 필요한 표면 마감 등 부품의 기능에 따라 올바른 선택이 결정됩니다.
이 글에서는 회주철과 연성 주철이 구조, 성능, 비용 면에서 어떻게 다른지 실용적인 분석을 제공합니다. 엔지니어링 인사이트와 실제 적용 사례를 바탕으로 프로젝트에 가장 신뢰할 수 있는 재료를 선택하는 데 도움이 될 것입니다.
흑연 구조: 성능 차이의 근원
회색 주철과 연성 주철은 모두 흑연 주철이지만, 흑연의 모양이 모든 것을 결정합니다.
- 회색 철 에는 금속 매트릭스를 파쇄하고 인장 강도를 감소시키는 플레이크 형태의 흑연이 포함되어 있습니다. 이러한 플레이크는 작은 균열처럼 작용하여 강도에는 좋지 않지만 가공 중 진동을 흡수하고 칩을 깨뜨리는 데는 탁월합니다.
- 연성 철 은 흑연을 구형 결절로 변형시킵니다. 이러한 둥근 내포물은 매트릭스의 연속성을 유지하여 인장 강도, 연신율 및 내충격성을 훨씬 더 높일 수 있습니다. 이러한 구조적 장점 덕분에 연성 철은 높은 기계적 응력이나 동적 하중을 받는 부품에 적합합니다.
간단히 말해서
플레이크는 스트레스를 끊고 → 결절은 스트레스를 전달합니다.
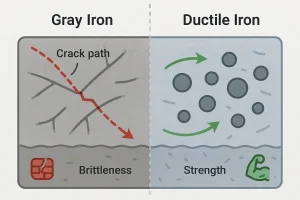
회철의 흑연은 조각을 형성하고 연성 철은 결절을 형성하여 강도와 성능에 영향을 미칩니다.
기계적 성능: 강도, 연신율 및 내충격성
주철 부품의 기계적 특성은 하중 하에서 작동하는 방식을 정의합니다. 회주철과 연성 주철의 가장 중요한 차이점은 다음과 같습니다:
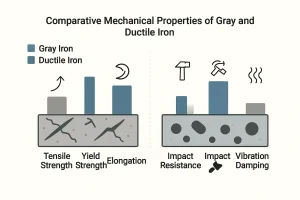
회주철과 연성철의 인장 강도, 항복 강도, 연신율을 비교한 막대 차트입니다.
속성 | 회색 철 | 연성 철 |
---|---|---|
흑연 양식 | 플레이크 흑연 | 구상 흑연 |
인장 강도 | 150-400 MPa | 400-700 MPa |
수율 강도 | 정의되지 않음(부서지기 쉬움) | 250-500 MPa |
휴식 시 신장 | < 1% | 10-18% |
내충격성 | 매우 낮음(노치 민감) | 높음(낮은 온도에서도) |
- 회색 철 은 세라믹처럼 작동합니다. 압축 시에는 강하지만 장력이나 충격에 의해 균열이 생기기 쉽습니다.
- 연성 철 연강처럼 연성, 탄력성이 뛰어나며 예고 없이 고장날 가능성이 훨씬 적습니다.
부품이 동적이거나 불규칙한 하중을 받을 수 있는 경우 연성 철이 더 안전한 엔지니어링 선택입니다.
진동 감쇠 및 음향 거동
그레이 아이언이 탁월한 분야 중 하나는 진동 감쇠입니다. 플레이크 흑연 구조는 소리와 진동파를 차단하여 내부에서 에너지를 발산합니다. 따라서 그레이 아이언은 다음과 같은 용도에 이상적입니다:
- 공작 기계 베이스
- 전기 모터 하우징
- 펌프 및 컴프레서 블록
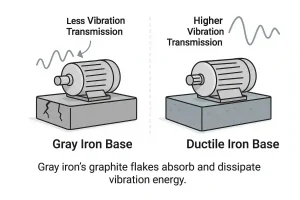
회색 철은 흑연 조각으로 인해 진동을 더 잘 흡수하므로 모터 하우징과 기계 베이스에 이상적입니다.
이러한 경우 성능은 강도가 아니라 안정성이 중요합니다. 진동, 진동, 공진하는 구성 요소는 치수의 부정확성, 소음, 피로를 유발할 수 있습니다.
연성 철는 더 강하지만 감쇠력이 떨어집니다. 결상 흑연은 진동 에너지를 보다 직접적으로 전달하므로 고정밀 애플리케이션에서 2차 진동 제어 조치가 필요할 수 있습니다.
주조성, 기계 가공성 및 파운드리 고려 사항
제조 관점에서 회주철은 더 관대한 소재입니다. 유동성이 뛰어나 벽이 얇고 복잡한 금형을 결함이 적은 상태로 채울 수 있습니다. 또한 냉각 속도 변화에 덜 민감합니다.
회색 철을 가공하는 것도 더 쉽습니다:
- 플레이크 흑연은 내장된 칩 브레이커 및 윤활제 역할을 합니다.
- 특히 고속 가공 작업에서 공구 수명이 더 길어집니다.
- 일반적으로 표면 마감이 우수합니다.
연성 주철은 비교적 잘 주조되지만 보다 견고한 게이팅 및 라이저 설계가 필요할 수 있습니다. 높은 경도와 결절 구조는 공구 마모와 절삭 저항을 증가시키지만, 적절한 공구와 이송을 사용하면 이러한 영향을 최소화할 수 있습니다.
부품에 광범위한 가공이 필요하거나 형상이 복잡한 경우 회색 철을 사용하면 생산 비용을 절감할 수 있습니다.
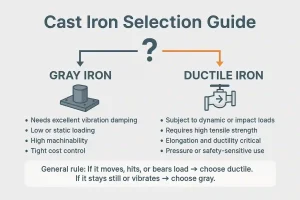
애플리케이션 유형에 따라 회색 또는 연성 다리미를 선택하는 방법에 대한 빠른 참조 가이드입니다.
비용 고려 사항
주조 프로젝트에서 비용은 단순히 재료 가격만 고려하는 것이 아니라 완성된 부품당 총 비용을 고려합니다.
회색 철 는 분명한 비용 이점이 있습니다:
- 원자재 비용 절감
- 결절화 첨가제(예: 마그네슘)가 필요 없음
- 캐스팅 중 필요한 프로세스 제어 감소
- 더 빠르고 경제적인 가공
연성 철 는 추가 단계를 소개합니다:
- 구상 흑연 형성을 위한 처리
- 제어할 프로세스 변수(온도, 접종 타이밍)가 더 많아졌습니다.
- 경도가 높을수록 가공 시간 및 공구 마모가 증가합니다.
예산이 빠듯한 대량 생산 부품의 경우 그레이 아이언을 사용하면 복잡성에 따라 15~25%의 비용을 절감할 수 있습니다. 하지만 그레이 아이언 부품이 피로나 충격으로 인해 고장이 나면 초기 절감 효과는 금방 사라집니다.
실제 사례: 독일 오프로드 차량의 기어 하우징
독일의 오프로드 기계 제조업체인 유럽 고객사 중 한 곳은 처음에 기어 하우징 부품으로 회주철을 선택했습니다. 그러나 토크 진동과 갑작스러운 하중 충격에 반복적으로 노출되면서 조기 균열이 발생했습니다.
로 전환한 후 EN-GJS-500-7 연성 인두구성 요소의 서비스 수명이 2배 이상 증가했습니다. 40%를 사용하여 12% 생산 비용 상승. 이러한 개선으로 보증 클레임이 크게 감소하고 운영 안정성이 향상되었으며 궁극적으로 총 소유 비용이 절감되었습니다.
중요한 애플리케이션에서 연성 철의 높은 재료 비용은 성능 수명과 안전 마진으로 상쇄되는 경우가 많습니다.
애플리케이션 기반 선택 가이드
회색 철과 연성 철을 결정하는 가장 좋은 방법은 소재 선호도가 아닌 기능부터 시작하는 것입니다.
애플리케이션 유형 | 추천 자료 | 이유 |
---|---|---|
기계 프레임, 모터 하우징 | 회색 철 | 높은 댐핑, 정적 부하 |
펌프 본체, 브레이크 로터 | 회색 철 | 주조성, 내마모성 |
유압 밸브, 기어 하우징 | 연성 철 | 압력, 충격 하중 |
서스펜션 암, 파이프 피팅 | 연성 철 | 높은 스트레스, 안전이 중요한 사용 |
큰 단면 또는 고르지 않은 지오메트리 | 연성 철 | 구조적 응집력 향상 |
아직 잘 모르시겠어요? 일반적인 규칙은 다음과 같습니다:
- 움직이거나 부딪히거나 하중을 견디는 경우 → 연성을 선택합니다.
- 가만히 있거나 진동이 있거나 가공이 필요한 경우 → 회색을 선택합니다.
주철 생산 역량
당사는 유럽 산업 고객을 중심으로 국제 표준에 따라 회주물 및 연성 주물을 모두 제조합니다.
제공되는 자료:
- 그레이 아이언: EN-GJL-150 ~ EN-GJL-300
- 연성 다리미: EN-GJS-400-15, EN-GJS-500-7, EN-GJS-600-3
서비스:
- 캐스팅 시뮬레이션 및 디자인 검토
- 미세 구조 검증 및 기계적 테스트
- CNC 가공 및 표면 마감
- 문서(EN10204 3.1, PPAP, 치수 보고서)
EU 및 영국 고객을 위한 수출용 패키징과 지원으로 프로토타입부터 생산까지 프로젝트를 지원합니다. 10개가 필요하든 10,000개가 필요하든, 우리 팀은 일관성과 기술적 자신감을 제공합니다.
결론: 소재 적합성은 성능 보험입니다
회색과 연성 철은 모두 고유한 장점을 제공합니다. 핵심은 소재의 특성을 기능적 요구사항에 맞추는 것입니다.
- 그레이 아이언은 진동, 비용 효율성, 가공 용이성 측면에서 최고의 선택입니다.
- 연성 철은 강도, 연성 및 동적 성능이 필수적인 곳에서 승리합니다.
올바른 등급을 선택하면 부품 성능에만 영향을 미치는 것이 아니라 평판, 일정, 예산도 보호할 수 있습니다.
자주 묻는 질문
Q1: 브레이크 로터에는 어떤 유형의 주철이 더 적합합니까?
일반적으로 내마모성과 진동 감쇠 특성이 뛰어난 회색 철이 선호됩니다.
Q2: 연성 철을 내압 부품에 사용할 수 있나요?
예. 연성 흑연은 구상 흑연 구조로 유압 밸브 및 서스펜션 암과 같은 가압 및 동적 하중 애플리케이션에 필요한 강도와 연신율을 제공합니다.
Q3: 연성 철보다 회주철이 가공하기 쉬운가요?
예. 회철의 플레이크 흑연은 천연 칩 브레이커 및 윤활제 역할을 하여 더 쉽고 경제적으로 가공할 수 있습니다.
주철 선택에 대한 전문가의 도움 받기
부품 설계를 평가하거나 올바른 소재를 선택하는 데 도움이 필요하신가요?
도면이나 기술 요구 사항을 보내주시면 안내, 권장 사항 및 경쟁력 있는 견적을 제공해 드립니다.
👉 지금 바로 문의하세요 를 클릭하여 시작하세요.