Faibles investissements en outillage et délais d'exécution rapides : Un avantage stratégique
Pour les grands composants métalliques, les coûts d'outillage et les délais d'exécution sont souvent des facteurs décisifs pour la faisabilité d'un projet. Le moulage en sable offre un avantage certain sur ces deux fronts, en particulier lorsque la flexibilité, la personnalisation et des cycles de production plus courts sont essentiels.
Contrairement au moulage sous pression ou au moulage à la cire perdue, qui nécessitent des moules en acier de haute précision pouvant coûter $20 000 ou plus, le moulage au sable utilise des moules temporaires fabriqués à partir de sable et de liants. Ces moules sont beaucoup moins coûteux à produire et peuvent généralement être préparés en quelques jours. Par exemple, le moulage d'un carter de boîte de vitesses d'un mètre dans le sable peut nécessiter un investissement en outillage de seulement $2 000, soit près d'un dixième du coût d'un moule métallique comparable.
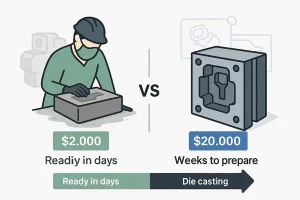
Visualisation côte à côte de la rentabilité du moulage en sable et de la rapidité du moulage sous pression
La vitesse n'est qu'une partie de l'équation. Les moules à sable peuvent être facilement ajustés ou reconstruites pour s'adapter aux changements de conception, ce qui rend le processus idéal pour les essais d'ingénierie, l'ingénierie inverse et les pièces fabriquées sur commande. Dans des secteurs comme l'exploitation minière, la marine et l'énergie, où les grands composants nécessitent souvent de multiples révisions ou un remplacement à la demande, ce niveau de flexibilité réduit à la fois les risques liés au projet et le gaspillage de capital.
Un moule permanent peut bloquer vos décisions de conception à un stade précoce. Un moule en sable vous donne la liberté d'évoluer.
Les avantages en un coup d'œil :
-
Investissement initial moins élevé pour le développement de moules
-
Délai d'exécution rapide de la CAO à la première coulée
-
Agilité de la conception avec des révisions ou des reconstructions peu coûteuses
Si votre plan de production comprend des lots de taille moyenne, des séries pilotes ou des itérations de conception à un stade avancé, le moulage en sable offre l'efficacité de l'outillage et la rapidité de réaction qu'exigent les flux de travail industriels modernes.
Liberté de conception : Prise en charge de géométries complexes à grande échelle
L'un des avantages les plus précieux, mais souvent sous-estimé, du moulage en sable est son exceptionnelle souplesse de conception, en particulier lorsqu'il s'agit de composants de grande taille et géométriquement complexes. Contrairement aux moules métalliques permanents, qui imposent des limites strictes en termes de forme, d'angle de dépouille et de plan de joint, les moules en sable sont formés à partir de modèles personnalisés et peuvent être adaptés pour prendre en charge pratiquement n'importe quelle géométrie.
Le moulage en sable s'adapte caractéristiques internes tels que les sections creuses, les nervures, les bossages et les canaux percés transversalement à l'aide de noyaux de sable amovibles.
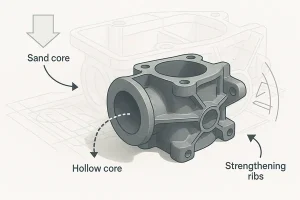
Le moulage en sable permet d'obtenir des caractéristiques complexes telles que des sections creuses et des nervures structurelles dans des composants de grande taille.
Ces caractéristiques peuvent être intégrées dans une seule coulée, ce qui élimine le besoin de soudage, d'assemblage ou d'étapes de moulage multiples. Les ingénieurs peuvent optimiser les performances structurelles, réduire le poids et simplifier l'usinage en aval, le tout sans compromettre la fabricabilité.
Cette capacité est particulièrement importante pour les composants de grande taille dans des applications exigeantes, telles que
-
- Corps de pompe avec voies d'écoulement intégrées
-
- Blocs moteurs avec galeries de refroidissement internes
-
- Moyeux d'éoliennes avec des cavités profondes à plusieurs axes
-
- Châssis de machines lourdes avec des nervures de renforcement encastrées
Les moules en sable étant jetables, les modifications de conception sont faciles et peu coûteuses à mettre en œuvre. Qu'il s'agisse de repositionner un trou de boulon, de modifier l'épaisseur d'une paroi ou d'adapter une bride, les ingénieurs peuvent procéder à des ajustements sans mettre au rebut un outillage coûteux. Cette flexibilité permet d'affiner la conception à un stade avancé, de réaliser des prototypes ou de procéder à des itérations rapides au cours des cycles de développement.
Une géométrie complexe ne doit pas être une contrainte, mais une opportunité de conception.
Dans les industries où la taille et la performance comptent autant que la précision, le moulage en sable permet aux ingénieurs de réaliser pleinement leur intention de conception. Il élimine les contraintes imposées par un outillage rigide et favorise l'innovation à grande échelle.
Compatible avec les alliages à haute température comme l'acier et la fonte ductile
Le moulage au sable excelle là où beaucoup d'autres méthodes échouent : la manipulation de métaux à point de fusion élevé tels que l'acier au carbone, l'acier allié et la fonte ductile. Ces matériaux sont essentiels pour les applications lourdes qui exigent solidité, résistance à la chaleur et longue durée de vie, mais ils posent de sérieux problèmes pour les processus de moulage qui reposent sur des moules permanents.
Le moulage sous pression, par exemple, est optimisé pour les alliages à bas point de fusion comme l'aluminium, le magnésium ou le zinc. Ses moules en acier ne peuvent tout simplement pas supporter les températures extrêmes - souvent supérieures à 1500°C (2730°F) - nécessaires pour couler de l'acier ou du fer en fusion.
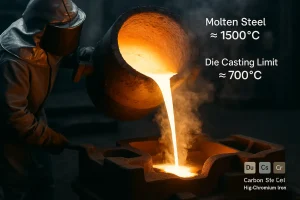
Le métal en fusion est coulé dans un moule en sable, adapté aux alliages à haute température tels que la fonte ductile et l'acier.
Même avec des systèmes de refroidissement, la fatigue thermique de l'outillage rend le moulage sous pression techniquement et économiquement impraticable pour ces métaux.
Le moulage en sable évite totalement ce problème. Grâce à l'utilisation de sable de silice ou de chromite résistant à la chaleur, les moules sont entièrement jetables et ne sont pas affectés par la température du métal en fusion. Ce procédé est donc idéal pour le moulage d'alliages ferreux, notamment :
-
- Fonte ductile pour les boîtiers de boîte de vitesses et les bras de suspension
-
- Acier faiblement allié pour les moyeux d'éoliennes et les châssis de transmission
-
- Fers à repasser à haute teneur en chrome pour des revêtements résistants à l'usure dans les équipements d'exploitation minière et de concassage
En raison de cette compatibilité, le moulage en sable est le choix par défaut pour les composants structurels et sous pression dans des secteurs tels que la production d'énergie, les machines hors route et l'ingénierie marine.
On ne choisit pas la fonte au sable uniquement pour la géométrie, mais lorsque le métal lui-même l'exige.
Lorsque votre projet exige des performances robustes dans des conditions de contrainte ou de chaleur élevées, le moulage en sable offre une flexibilité matérielle que d'autres méthodes ne peuvent tout simplement pas supporter.
Surmonter les défauts : Comment le moulage au sable moderne garantit la qualité
Le moulage au sable a toujours été associé à la rugosité de la surface, à la variabilité des dimensions et aux défauts internes. Mais dans les fonderies modernes, ces problèmes ne sont plus inhérents au processus : il s'agit de problèmes d'ingénierie avec des solutions connues et contrôlées.
Aujourd'hui, les flux de travail de moulage intègrent Simulation de solidification basée sur l'IAO, systèmes de moulage automatiséset les essais non destructifs (END) pour garantir la qualité des pièces, du modèle à l'inspection finale. Le résultat : des pièces moulées en sable qui répondent systématiquement aux spécifications industrielles les plus exigeantes.
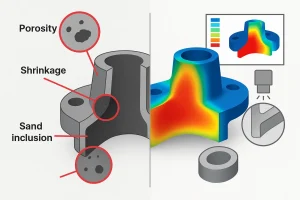
Visualisation côte à côte de la coulée de sable traditionnelle par essais et erreurs et de la simulation moderne pour une meilleure précision
Défauts courants et solutions modernes :
-
- Porosité et rétrécissement
Éliminé grâce à la modélisation de la solidification en 3D, à l'optimisation des colonnes montantes et aux courbes de refroidissement contrôlées.
- Porosité et rétrécissement
-
- Inclusion de sable
Prévention par une conception adéquate des portes, des systèmes de filtration et des procédures de nettoyage des moules.
- Inclusion de sable
-
- Distorsion ou déformation
Réduction grâce à un compactage uniforme du moule et à une application cohérente du liant
- Distorsion ou déformation
En simulant le flux thermique et la solidification du métal avant la première coulée, les ingénieurs peuvent identifier les zones à risque telles que les points chauds et garantir une géométrie de moule et une ventilation optimales. Cette approche proactive réduit considérablement les taux de défaut, en particulier pour les composants de grande taille et de masse élevée.
Exemple d'application :
Dans un récent projet de carter de boîte de vitesses pour un équipement minier, la simulation a révélé un risque de rétrécissement aux intersections des brides des boulons. Les ingénieurs ont repositionné les colonnes montantes et ajusté les voies de refroidissement. Résultat : un succès immédiat, vérifié par inspection ultrasonique (UT), sans qu'aucune retouche ne soit nécessaire.
Conclusion :
Le moulage moderne en sable est de qualité et contrôlé par le processus. Grâce à l'outillage numérique, aux diagnostics avancés et aux inspections rigoureuses (ultrasons, radiographie et ressuage), il offre des performances constantes pour les pièces critiques dans des secteurs tels que la production d'énergie, la construction et les transports.
Lorsque la précision rencontre la discipline du processus, le moulage en sable devient une solution fiable, et non un compromis.
Quand choisir le moulage au sable plutôt que d'autres méthodes
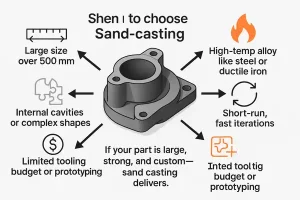
Guide visuel pour le choix du moulage en sable pour les composants de grande taille, personnalisés et à haute température.
Avec une large gamme de technologies de moulage disponibles - moulage sous pression, moulage à la cire perdue, moulage permanent - il est important de savoir quand le moulage en sable est le mieux adapté. Le choix dépend de plusieurs facteurs clés : la taille de la pièce, la géométrie, l'alliage, la quantité et la flexibilité de la conception.
Le moulage en sable est la meilleure option lorsque :
-
La pièce est volumineuse (généralement plus de 10 kg ou 500 mm).
-
Le matériau est un alliage à haute température comme l'acier ou la fonte ductile.
-
La conception comprend des caractéristiques internes complexes, des nervures ou des cavités.
-
Vous avez besoin d'une production en petite série, d'un prototypage rapide ou de pièces de rechange.
-
Des modifications de conception ou des personnalisations sont attendues à un stade avancé.
En revanche, moulage sous pression est idéal pour les petites et moyennes pièces en aluminium ou en zinc produites en très grande quantité avec une tolérance dimensionnelle serrée. Coulée en cire perdue est la meilleure solution pour les petites pièces complexes qui nécessitent un excellent état de surface, mais elle s'accompagne d'un coût unitaire plus élevé et d'un temps d'outillage plus long.
Le moulage au sable n'est pas seulement une solution de secours, c'est un processus stratégique pour la taille, la complexité et l'adaptabilité.
Note finale :
Si votre projet exige une résistance structurelle, une flexibilité d'ingénierie et une efficacité économique - sans s'engager dans un outillage à grand volume - le moulage sur sable est la solution qui s'aligne sur les besoins industriels du monde réel.
Découvrez nos capacités de moulage en sable ou contactez-nous pour un devis. Nous vous aiderons à évaluer la faisabilité et à optimiser les performances.