Comprendre les défauts de coulée dans la pratique de la fonderie
Les défauts de moulage sont des imperfections ou des irrégularités qui se produisent au cours du processus de moulage et qui peuvent compromettre l'intégrité structurelle, la précision des dimensions ou l'apparence du produit final. Dans les industries qui dépendent de composants de haute performance, comme l'automobile, la construction ou l'hydraulique, il est essentiel pour les producteurs et les acheteurs de comprendre comment et pourquoi ces défauts surviennent.
Ce guide présente les défauts de fonderie les plus fréquents rencontrés dans les pièces coulées en fonte ductile, en fonte grise et en acier. Pour chacun d'entre eux, nous couvrons les indicateurs visuels typiques, les causes sous-jacentes, les stratégies préventives et les remèdes possibles.
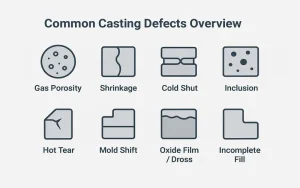
Aperçu visuel de huit types de défauts de fonderie courants, illustrés par des icônes et des étiquettes.
Porosité du gaz
Aspect typique : Petites cavités arrondies ou vides, soit à la surface, soit à l'intérieur du moulage. Elles sont particulièrement problématiques dans les composants sous pression tels que corps de pompe ou des corps de vanne.
👉 Remarque : des études industrielles indiquent que la porosité gazeuse et le retrait représentent ensemble jusqu'à 50% de tous les défauts de moulage, ce qui en fait les types les plus courants et les plus critiques à surveiller.
Les causes :
La porosité gazeuse dans les pièces moulées en fonte ductile et en acier résulte généralement de l'emprisonnement de gaz pendant la solidification. Ce phénomène peut être causé par :
- Humidité excessive dans les moules ou les matériaux de base
- Dégazage incomplet du métal en fusion
- Mauvaise ventilation du moule ou turbulences excessives pendant la coulée
- Utilisation de liants à haute teneur en résine qui se décomposent en gaz
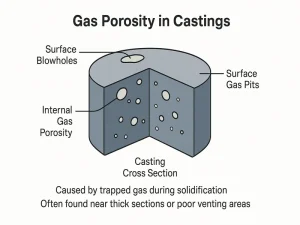
Aspect typique de la porosité gazeuse et des soufflures superficielles dans les pièces métalliques coulées en raison de l'air ou de l'humidité emprisonnés.
La prévention :
- S'assurer que les moules et les noyaux sont bien séchés
- Utiliser des matériaux de charge à faible teneur en hydrogène et de grande pureté
- Optimiser la conception des portes pour minimiser les turbulences
- Utiliser le dégazage à l'argon ou à l'azote pendant le traitement de la matière fondue
Solutions :
- La porosité mineure peut être traitée par réparation de la soudure ou par imprégnation.
- Pour les problèmes persistants, les logiciels de simulation peuvent aider à visualiser les flux de gaz et à améliorer la conception des moules.
Cavités de rétraction
Aspect typique : Les vides internes ou les zones enfoncées sont généralement situés dans les sections plus épaisses ou dans les zones éloignées de l'alimentation efficace de la colonne montante. Ils se produisent souvent dans les grandes boîtiers en fonte ductileou des plaques de base en acier.
👉 Remarque : les cavités de retrait sont particulièrement problématiques dans les pièces moulées structurelles, car elles peuvent entraîner des points de concentration de contraintes qui réduisent considérablement la résistance mécanique et la durée de vie en fatigue.
Les causes :
Les cavités de retrait se forment au cours de la phase finale de la solidification, lorsque le métal en fusion ne parvient pas à alimenter les régions qui se contractent encore. Les facteurs qui y contribuent sont les suivants :
- Elévateurs sous-dimensionnés ou mal positionnés
- Absence de contrôle directionnel de la solidification
- Congélation prématurée des cols d'alimentation
- Sections transversales épaisses avec des vitesses de refroidissement inégales
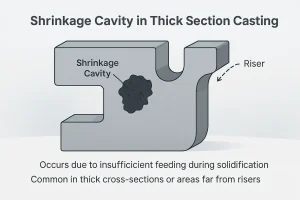
Une cavité de retrait typique causée par la solidification dans les sections épaisses
La prévention :
- Conception adéquate des colonnes montantes avec adaptation du module aux zones critiques
- Utilisation de refroidisseurs pour guider la dissipation de la chaleur
- Manchons isolants pour ralentir la solidification des colonnes montantes
- Ajuster l'orientation de la coulée pour favoriser la solidification du haut vers le bas
Solutions :
- Modifier la géométrie de la coulée ou augmenter le volume d'alimentation
- Réparer les cavités par soudage à l'arc ou par pulvérisation de métal (lorsque les spécifications le permettent).
Fermeture à froid (erreur de parcours)
Aspect typique : Discontinuités minces et linéaires ou joints non fusionnés aux jonctions où deux fronts métalliques n'ont pas fusionné. Souvent observées dans les pièces moulées à parois mincesLes joints horizontaux, les géométries complexes ou les joints horizontaux.
👉 Note : Bien que les fermetures à froid soient généralement visibles en surface, elles peuvent également former des fissures internes dans les zones critiques, compromettant potentiellement les surfaces d'étanchéité ou provoquant une défaillance prématurée sous pression.
Les causes :
Les fermetures à froid se produisent lorsque des flux de métal partiellement solidifiés se rencontrent mais ne fusionnent pas en raison de.. :
- Faibles températures de coulée
- Mauvaise fluidité de l'alliage
- Longs trajets d'écoulement ou angles vifs dans la conception des moules
- Perte de chaleur importante à travers les noyaux ou les refroidissements métalliques
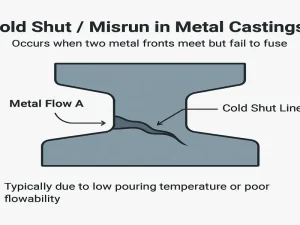
Le défaut de fermeture à froid se produit lorsque deux fronts de métal en fusion ne parviennent pas à fusionner correctement, laissant une ligne ou un joint visible.
La prévention :
- Augmentation de la température de coulée dans les limites spécifiques à l'alliage
- Réduire la longueur de l'écoulement en déplaçant les vannes plus près des zones critiques
- Utiliser des transitions arrondies et des filets dans la conception des motifs
- Éviter les injecteurs sous-dimensionnés qui limitent le débit.
Solutions :
- Modifier le système de vannes pour réduire les pertes de vitesse
- Améliorer la sélection des alliages ou utiliser des inoculants améliorant le débit
- Si l'intégrité structurelle n'est pas compromise, une réparation localisée peut être possible.
Inclusions (scories / sables / oxydes)
Aspect typique : Particules sombres ou cassantes incrustées dans la pièce moulée, visibles sur les surfaces usinées ou lors d'un contrôle par END. Elles peuvent provenir de scories, de sable érodé ou de films d'oxyde.
👉 Remarque : les inclusions sont parmi les défauts les plus difficiles à détecter rapidement, car elles restent souvent cachées jusqu'à ce que l'usinage ou la défaillance en service se produise, en particulier dans les applications à haute pression ou sensibles à la fatigue.
Les causes :
Les inclusions non métalliques proviennent de diverses sources de contamination :
- Élimination incomplète du laitier lors de la manipulation de la matière fondue
- Érosion du sable dans la cavité du moule pendant le remplissage
- Réoxydation causée par la turbulence des métaux
- Sections de noyau détachées ou revêtement insuffisant sur les parois du moule
La prévention :
- Utiliser des conditionneurs de scories et procéder à un écrémage minutieux de la poche de coulée.
- Introduire des filtres en mousse céramique dans les ingates
- Maintien de la résistance du moule et de l'état de surface
- Réduire la hauteur de déversement pour minimiser les éclaboussures et les turbulences
Solutions :
- Les inclusions superficielles peuvent être éliminées par usinage
- Les inclusions profondes nécessitent un rejet ou une refonte, en particulier dans les pièces structurelles critiques.
- Les audits métallurgiques permettent de retracer les types d'inclusion à des étapes spécifiques du processus.
Déchirures chaudes / Fissures thermiques
Aspect typique : Fissures dentelées ou ramifiées, se produisant généralement dans les angles vifs, les bossages ou les jonctions d'épaisseur de paroi variable. Ces défauts se forment au cours des dernières étapes de la solidification, lorsque la pièce moulée ne peut pas supporter les contraintes thermiques internes.
Les causes :
Les déchirures à chaud sont souvent le résultat d'une contrainte mécanique ou d'une mauvaise collapsibilité du moule. Les principaux facteurs contributifs sont les suivants :
- Changements brusques de l'épaisseur de la paroi
- Moules en sable rigides et peu susceptibles de s'effondrer
- Températures de coulée élevées entraînant des intervalles de solidification importants
- Filets ou éléments de soulagement des contraintes inadéquats dans la conception
La prévention :
- Épaisseur de paroi uniforme et transitions géométriques douces
- Matériaux de moulage améliorés ou additifs améliorant la collapsibilité
- Contrôle de la température de coulée et du préchauffage du moule
- Inclusion d'encoches de décharge et d'âmes flexibles
Solutions :
- Les fissures mineures peuvent être réparées par soudage (si les spécifications le permettent).
- La correction à long terme implique généralement une nouvelle conception géométrique ou l'utilisation d'autres matériaux de moulage.
Déplacement du moule / Déplacement du noyau
Aspect typique : Surfaces en escalier ou désalignement dimensionnel entre les différentes moitiés de la pièce moulée, entraînant des épaisseurs de paroi incohérentes ou des trous décalés.
Les causes :
Le déplacement du moule est causé par un mauvais alignement entre la chape et la traînée, ou par le mouvement des noyaux internes. Ce phénomène peut être dû à
- Force de serrage insuffisante ou ajustement trop lâche du flacon
- Usure du motif ou goujons endommagés
- Pression métallostatique élevée ou secousses lors de la coulée
La prévention :
- Renforcer les fixations des moules et assurer un enregistrement précis des moules
- Remplacer l'équipement de patronage et les noyaux d'impression usés
- Ajuster la hauteur de versement pour réduire la pression du métal
Solutions :
- L'usinage peut être possible si les tolérances le permettent
- Reconstruction ou mise à niveau des systèmes d'alignement et d'outillage des modèles
Films d'oxyde / défauts de crasse
Aspect typique : Couches minces, semblables à un film, ou flocons fragiles près de la surface de la pièce moulée, souvent découverts seulement lors de l'usinage ou de l'analyse métallographique. Ces inclusions affaiblissent la résistance à la fatigue.
Les causes :
Les défauts liés à l'oxyde se forment en raison de :
- Exposition du métal en fusion à l'oxygène pendant la coulée
- Turbulences excessives dans le système de portillon
- Réoxydation causée par une manipulation inadéquate de la poche de coulée ou par un retard
La prévention :
- Utiliser une atmosphère protectrice (argon) ou un flux pour réduire l'oxydation.
- Optimiser la géométrie des vannes pour permettre un écoulement laminaire
- Minimiser les turbulences du métal en contrôlant la vitesse de coulée
Solutions :
- L'oxyde superficiel peut parfois être éliminé par usinage
- Les oxydes internes profonds nécessitent une refonte et une révision du gating
- Les outils d'analyse thermique peuvent aider à optimiser la pratique de la fonte
Remplissage incomplet (sous-remplissage)
Aspect typique : Sections manquantes, coins incomplets ou remplissages courts dans les pièces moulées, en particulier dans les pièces à parois minces ou à grande surface.
Les causes :
Ce défaut est dû au fait que le métal en fusion ne remplit pas complètement la cavité du moule avant de se solidifier. Les raisons les plus courantes sont les suivantes
- Température d'écoulement basse ou mauvaise fluidité
- Conception de vannes qui restreignent le flux ou induisent des turbulences précoces
- Contre-pression de gaz due à une mauvaise ventilation
- Caractéristiques des moules trop complexes
La prévention :
- Augmenter la température de coulée dans les limites de l'alliage
- Amélioration du taux d'ouverture et de l'évacuation de l'air dans la cavité du moule
- Simplifier la géométrie de la coulée ou la diviser en plusieurs parties
- Appliquer les techniques d'assistance par le vide, le cas échéant
Solutions :
- Évaluer les simulations de remplissage pour localiser les zones problématiques
- Refonte avec correction des systèmes d'écoulement et d'aération
Méthodes de contrôle non destructif des défauts de fonderie
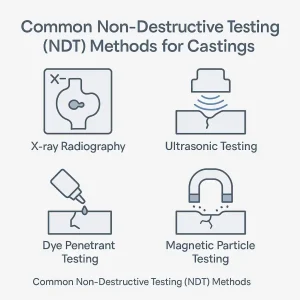
Méthodes CND couramment utilisées pour l'inspection des pièces de fonderie : Rayons X, ultrasons, ressuage et magnétoscopie.
Méthode d'essai | Défauts détectables | Matériaux et utilisations appropriés | Notes |
---|---|---|---|
Radiographie à rayons X | Retrait interne, porosité, vides | Pièces moulées complexes, pièces à parois épaisses | Excellent détail ; plus cher |
Contrôle par ultrasons | Fissures souterraines, inclusions | Grandes sections, acier/fonte ductile | Nécessite des compétences d'opérateur et une bonne surface |
Essai de ressuage | Fissures superficielles, fermetures à froid | Métaux non poreux (aluminium, acier) | Simple, abordable ; seulement visible en surface |
Particule magnétique | Défauts en surface et près de la surface | Métaux ferreux (fonte, acier) | Rapide et fiable ; limité aux pièces magnétiques |
Ces méthodes d'essai permettent d'identifier les défauts internes ou externes avant l'usinage ou la livraison, garantissant ainsi que vos composants moulés répondent aux spécifications en matière de dimensions et de performances.
Réflexions finales
Les défauts de fonderie peuvent affecter de manière significative les performances, les coûts et la satisfaction des clients. En comprenant clairement les causes de chaque défaut et les stratégies correctives, les fonderies et les acheteurs peuvent jouer un rôle proactif dans l'assurance qualité.
Vous avez besoin d'une assistance technique ou d'une analyse des défauts ? Contacter notre équipe pour obtenir des conseils d'experts et des solutions de moulage sur mesure.