Verständnis von Gussfehlern in der Gießereipraxis
Gussfehler sind Fehler oder Unregelmäßigkeiten, die während des Gießprozesses auftreten und die strukturelle Integrität, die Maßhaltigkeit oder das Aussehen des Endprodukts beeinträchtigen können. In Branchen, die auf Hochleistungskomponenten angewiesen sind - wie z. B. die Automobil-, Bau- oder Hydraulikindustrie - ist es sowohl für Hersteller als auch für Käufer von entscheidender Bedeutung zu verstehen, wie und warum diese Fehler entstehen.
Dieser Leitfaden beschreibt die häufigsten Gussfehler, die bei Gussstücken aus duktilem Eisen, Grauguss und Stahl auftreten. Für jeden dieser Gussfehler werden typische visuelle Indikatoren, die zugrundeliegenden Ursachen, Präventionsstrategien und mögliche Abhilfemaßnahmen beschrieben.
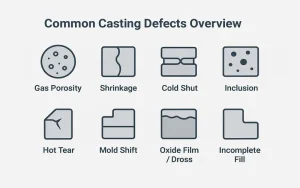
Visuelle Übersicht über acht häufige Gussfehlerarten, illustriert mit Symbolen und Beschriftungen.
Gas Porosität
Typisches Aussehen: Kleine, abgerundete Hohlräume oder Lücken entweder an der Oberfläche oder im Gussteil. Diese sind besonders problematisch bei drucktragenden Bauteilen wie Pumpengehäuse oder Ventilkörper.
👉 Hinweis: Industriestudien zeigen, dass Gasporosität und Schrumpfung zusammen bis zu 50% aller Gussfehler ausmachen, was sie zu den häufigsten und kritischsten zu überwachenden Fehlerarten macht.
Die Ursachen:
Gasporosität in Gussstücken aus duktilem Eisen und Stahl entsteht in der Regel durch Gaseinschlüsse während der Erstarrung. Dies kann verursacht werden durch:
- Übermäßige Feuchtigkeit in der Form oder im Kernmaterial
- Unvollständige Entgasung von geschmolzenem Metall
- Schlechte Entlüftung der Form oder übermäßige Turbulenzen beim Gießen
- Verwendung von Bindemitteln mit hohem Harzgehalt, die sich in Gas zersetzen
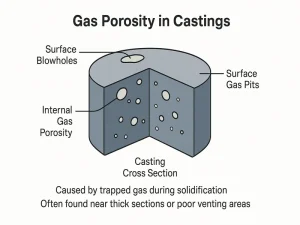
Typisches Erscheinungsbild von Gasporosität und Oberflächenlunkern in Metallgussstücken aufgrund von eingeschlossener Luft oder Feuchtigkeit.
Prävention:
- Sicherstellen, dass Formen und Kerne gründlich getrocknet sind
- Verwendung wasserstoffarmer, hochreiner Ladungsmaterialien
- Optimiertes Anschnittdesign zur Minimierung von Turbulenzen
- Einsatz von Argon- oder Stickstoffentgasung bei der Schmelzebehandlung
Lösungen:
- Geringe Porosität kann durch Schweißnahtreparatur oder Imprägnierung behoben werden.
- Bei hartnäckigen Problemen kann Simulationssoftware helfen, die Gasströmung zu visualisieren und die Werkzeugkonstruktion zu verbessern.
Schrumpfung Hohlräume
Typisches Aussehen: Innere Hohlräume oder eingesunkene Bereiche, die sich typischerweise in dickeren Abschnitten oder in Bereichen befinden, die weit von einer effektiven Speisung des Speisers entfernt sind. Diese treten häufig in großen Gehäuse aus duktilem Gusseisen, Lagerböcke oder Stahlgrundplatten.
👉 Hinweis: Lunker sind vor allem bei Gussteilen problematisch, da sie zu Spannungskonzentrationen führen können, die die mechanische Festigkeit und Ermüdungslebensdauer erheblich verringern.
Die Ursachen:
Lunker entstehen in der letzten Phase der Erstarrung, wenn das geschmolzene Metall nicht in die noch schrumpfenden Bereiche eindringt. Dazu tragen unter anderem folgende Faktoren bei:
- Unterdimensionierte oder schlecht positionierte Steigleitungen
- Fehlen einer gerichteten Erstarrungskontrolle
- Vorzeitiges Einfrieren von Fütterungshälsen
- Dicke Querschnitte mit ungleichmäßigen Abkühlungsraten
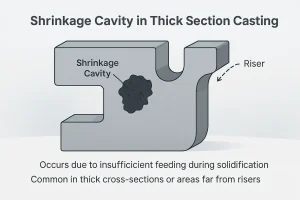
Ein typischer Schwindungshohlraum, der durch Erstarrung in dicken Profilen entsteht
Prävention:
- Richtiges Speiserdesign mit Anpassung des Moduls an kritische Zonen
- Verwendung von Kühlmitteln zur Steuerung der Wärmeableitung
- Isoliermanschetten zur Verlangsamung der Verfestigung des Steigrohrs
- Anpassung der Gussausrichtung zur Förderung der Erstarrung von oben nach unten
Lösungen:
- Änderung der Gussgeometrie oder Erhöhung des Speiservolumens
- Ausbessern von Hohlräumen durch Lichtbogenschweißen oder Metallspritzen (sofern nach Spezifikation zulässig)
Cold Shut (Misrun)
Typisches Aussehen: Dünne, lineare Diskontinuitäten oder nicht verschmolzene Nähte an Verbindungsstellen, an denen zwei Metallfronten nicht ineinander übergegangen sind. Oft zu sehen in dünnwandige Gussteilekomplexen Geometrien oder an horizontalen Fugen.
👉 Hinweis: Kaltverformungen sind zwar in der Regel an der Oberfläche sichtbar, können aber in kritischen Bereichen auch innere Risse bilden, die die Dichtflächen beeinträchtigen oder unter Druck zu einem vorzeitigen Versagen führen können.
Die Ursachen:
Kaltverschlüsse treten auf, wenn teilweise erstarrte Metallströme aufeinandertreffen, aber nicht verschmelzen können:
- Niedrige Gießtemperaturen
- Schlechte Fließfähigkeit der Legierung
- Lange Fließwege oder scharfe Ecken in der Formgestaltung
- Hoher Wärmeverlust durch Kerne oder Metallkühler
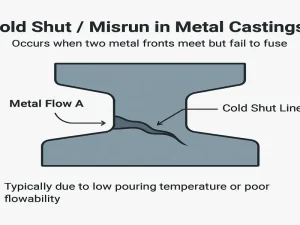
Ein Kaltverschlussfehler tritt auf, wenn zwei geschmolzene Metallfronten nicht richtig verschmelzen und eine sichtbare Linie oder Naht hinterlassen.
Prävention:
- Erhöhung der Gießtemperatur innerhalb der legierungsspezifischen Grenzen
- Verkürzung der Fließstrecke durch Verlegung der Schieber näher an kritische Bereiche
- Abgerundete Übergänge und Verrundungen in der Mustergestaltung verwenden
- Vermeiden Sie unterdimensionierte Einlässe, die die Durchflussmenge einschränken.
Lösungen:
- Änderung des Anschnittsystems zur Verringerung des Geschwindigkeitsverlusts
- Verbesserung der Legierungsauswahl oder Verwendung von fließverbessernden Inokulanzien
- Wenn die strukturelle Integrität nicht beeinträchtigt ist, kann eine lokale Reparatur möglich sein.
Einschlüsse (Schlacke / Sand / Oxide)
Typisches Aussehen: Dunkle oder spröde Partikel, die in das Gussteil eingebettet sind und auf bearbeiteten Oberflächen oder bei der ZfP-Prüfung sichtbar werden. Diese können von Schlacke, erodiertem Sand oder Oxidschichten herrühren.
👉 Hinweis: Einschlüsse gehören zu den am schwierigsten zu erkennenden Defekten, da sie oft verborgen bleiben, bis es zu einer Bearbeitung oder einem Ausfall während des Betriebs kommt - insbesondere bei Anwendungen, die unter hohem Druck stehen oder auf Ermüdung reagieren.
Die Ursachen:
Nichtmetallische Einschlüsse entstehen durch verschiedene Kontaminationsquellen:
- Unvollständige Schlackenentfernung bei der Schmelzebehandlung
- Sandauswaschung aus dem Formhohlraum während des Füllens
- Reoxidation durch Metallverwirbelung
- Lose Kernstücke oder unzureichende Beschichtung der Formwände
Prävention:
- Verwendung von Schlackenkonditionierern und gründliches Abschöpfen der Pfanne
- Einführung von Schaumkeramikfiltern an den Einlässen
- Beibehaltung einer gleichmäßigen Formfestigkeit und Oberflächenbeschaffenheit
- Reduzieren Sie die Gießhöhe, um Spritzer und Turbulenzen zu minimieren.
Lösungen:
- Oberflächeneinschlüsse können durch Bearbeitung entfernt werden.
- Tiefe Einschlüsse erfordern Ausschluss oder Neuguss, insbesondere bei kritischen Strukturteilen
- Metallurgische Audits können Einschlussarten zu bestimmten Prozessschritten zurückverfolgen
Heiße Risse / Thermorisse
Typisches Aussehen: Gezackte oder verzweigte Risse, die in der Regel an scharfen Ecken, Vorsprüngen oder Verbindungsstellen mit unterschiedlicher Wandstärke auftreten. Diese Fehler entstehen in den letzten Phasen der Erstarrung, wenn das Gussteil die inneren thermischen Spannungen nicht aufnehmen kann.
Die Ursachen:
Heiße Risse sind oft das Ergebnis von mechanischer Einschränkung oder schlechter Einfallfähigkeit der Form. Zu den wichtigsten Faktoren gehören:
- Abrupte Veränderungen der Wanddicke
- Starre Sandformen mit geringer Einfallgeschwindigkeit
- Hohe Gießtemperaturen führen zu großen Erstarrungsintervallen
- Unzureichende Verrundungen oder Spannungsentlastungsmerkmale in der Konstruktion
Prävention:
- Gleichmäßige Wandstärke und glatte geometrische Übergänge
- Verbesserte Formmaterialien oder Zusatzstoffe, die die Einfallfähigkeit erhöhen
- Kontrolle der Gießtemperatur und Vorwärmung der Form
- Einarbeitung von Entlastungskerben und flexiblen Kernen
Lösungen:
- Kleinere Risse können durch Schweißen repariert werden (wenn die Spezifikationen dies zulassen).
- Langfristige Korrekturen erfordern in der Regel eine geometrische Umgestaltung oder alternative Formmaterialien.
Formverschiebung / Kernverschiebung
Typisches Aussehen: Gestufte Oberflächen oder Maßabweichungen zwischen verschiedenen Gussstückhälften, die zu ungleichmäßigen Wandstärken oder versetzten Bohrungen führen.
Die Ursachen:
Die Formverschiebung wird durch einen Versatz zwischen Ober- und Unterteil oder durch die Bewegung der inneren Kerne verursacht. Dies kann auftreten aufgrund von:
- Unzureichende Spannkraft oder lockerer Sitz der Küvette
- Abnutzung des Musters oder beschädigte Passstifte
- Hoher metallostatischer Druck oder Rütteln beim Gießen
Prävention:
- Verstärkung der Kolbenbefestigung und Gewährleistung einer genauen Formregistrierung
- Ersetzen Sie verschlissene Modelleinrichtungen und Kerndrucke
- Gießhöhe einstellen, um den Metalldruck zu verringern
Lösungen:
- Eine maschinelle Bearbeitung ist möglich, wenn die Toleranzen dies zulassen.
- Umbau oder Aufrüstung von Modellierwerkzeugen und Ausrichtungssystemen
Oxidschichten / Krätzendefekte
Typisches Aussehen: Dünne, filmartige Schichten oder spröde Flocken in der Nähe der Gussoberfläche, die oft erst bei der Bearbeitung oder bei der metallografischen Analyse entdeckt werden. Diese Einschlüsse schwächen die Ermüdungsfestigkeit.
Die Ursachen:
Oxidbedingte Defekte entstehen durch:
- Exposition von geschmolzenem Metall gegenüber Sauerstoff während des Gießens
- Übermäßige Turbulenzen im Angusssystem
- Reoxidation durch unsachgemäße Handhabung der Pfanne oder Verzögerung
Prävention:
- Verwenden Sie eine Schutzatmosphäre (Argon) oder ein Flussmittel, um die Oxidation zu verringern.
- Optimierung der Anschnittgeometrie, um eine laminare Strömung zu ermöglichen
- Minimierung von Metallturbulenzen durch kontrollierte Gießgeschwindigkeit
Lösungen:
- Oberflächenoxid kann manchmal durch Bearbeitung entfernt werden.
- Tiefe innere Oxide erfordern Neufassung und Anschnittrevision
- Thermische Analysetools können zur Optimierung der Schmelzpraxis beitragen
Unvollständige Füllung (Unterfüllung)
Typisches Aussehen: Fehlende Abschnitte, unvollständige Ecken oder kurze Füllungen in Gussteilen - insbesondere bei dünnwandigen oder großflächigen Teilen.
Die Ursachen:
Dieser Fehler wird dadurch verursacht, dass das geschmolzene Metall den Formhohlraum nicht vollständig ausfüllt, bevor es erstarrt. Häufige Gründe sind:
- Niedrige Gießtemperatur oder schlechte Fließfähigkeit
- Anschnittdesign, das die Strömung einschränkt oder frühzeitige Turbulenzen hervorruft
- Gasrückstau durch schlechte Entlüftung
- Übermäßig komplexe Formmerkmale
Prävention:
- Erhöhung der Gießtemperatur innerhalb der Legierungsgrenzen
- Verbesserung des Anschnittverhältnisses und der Entlüftung des Formhohlraums
- Vereinfachung der Gussgeometrie oder Aufteilung in mehrteilige Konstruktionen
- Anwendung von Techniken zur Vakuumunterstützung, wo anwendbar
Lösungen:
- Auswertung von Füllsimulationen zur Lokalisierung problematischer Zonen
- Neufassung mit korrigierten Durchfluss- und Entlüftungssystemen
Methoden der zerstörungsfreien Prüfung von Gussfehlern
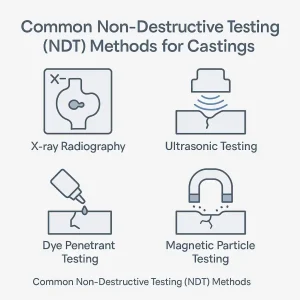
Gängige NDT-Methoden für die Gussprüfung: Röntgen, Ultraschall, Farbeindringprüfung und Magnetpulverprüfung.
Prüfverfahren | Erkennbare Defekte | Geeignete Materialien / Verwendungszwecke | Anmerkungen |
---|---|---|---|
Röntgenaufnahme | Innere Schrumpfung, Porosität, Hohlräume | Komplexe Gussteile, dickwandige Teile | Ausgezeichnete Details; teurer |
Ultraschallprüfung | Unterirdische Risse, Einschlüsse | Große Profile, Stahl/duktiles Eisen | Erfordert Geschicklichkeit des Bedieners und eine gute Oberfläche |
Farbeindringprüfung | Oberflächenrisse, Kaltverschlüsse | Nicht-poröse Metalle (Aluminium, Stahl) | Einfach, erschwinglich; nur an der Oberfläche sichtbar |
Magnetisches Teilchen | Oberflächenfehler und oberflächennahe Fehler | Eisenmetalle (Gusseisen, Stahl) | Schnell und zuverlässig; beschränkt auf magnetische Teile |
Diese Prüfverfahren helfen dabei, innere oder äußere Mängel vor der Bearbeitung oder Auslieferung zu erkennen, um sicherzustellen, dass Ihre Gussteile die Maß- und Leistungsspezifikationen erfüllen.
Abschließende Überlegungen
Gussfehler können Leistung, Kosten und Kundenzufriedenheit erheblich beeinträchtigen. Mit einem klaren Verständnis der Fehlerursachen und Abhilfestrategien können Gießereien und Einkäufer gleichermaßen eine proaktive Rolle bei der Qualitätssicherung übernehmen.
Benötigen Sie technische Unterstützung oder eine Fehleranalyse? Kontakt zu unserem Team für fachkundige Beratung und maßgeschneiderte Gusslösungen.