鋳造実務における鋳造欠陥の理解
鋳造欠陥とは、鋳造プロセス中に発生する欠陥や不規則性のことで、最終製品の構造的完全性、寸法精度、外観を損なう可能性があります。自動車、建築、油圧機器などの高性能部品に依存する業界では、このような欠陥がどのように発生するのか、またなぜ発生するのかを理解することは、生産者と購買者の双方にとって非常に重要です。
このガイドでは、ダクタイル鋳鉄、ねずみ鋳鉄、鋼鉄鋳物で最も頻繁に発生する鋳造欠陥について概説しています。それぞれについて、典型的な視覚的指標、根本的な原因、予防策、可能な対処法を取り上げています。
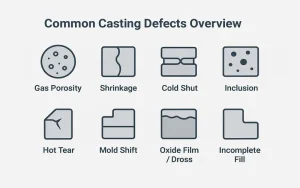
一般的な8種類の鋳造欠陥をアイコンとラベルで視覚的に説明。
ガス気孔率
典型的な外観: 鋳物の表面または内部にある、丸みを帯びた小さな空洞。これらは、以下のような保圧部品で特に問題となる。 ポンプハウジング またはバルブボディ。
👉 注:業界の調査によると、ガスポロシティと引けを合わせると、全鋳造欠陥の最大50%を占め、監視すべき最も一般的で重要なタイプとなっています。
原因がある:
ダクタイル鋳鉄や鋼鋳物におけるガスポロシティは、一般的に凝固中のガス巻き込みに起因する。この原因は以下の通りである:
- 金型や芯材に過度の水分が含まれている
- 溶融金属の不完全なガス抜き
- 鋳型の通気不良または注湯中の過度の乱流
- 分解してガスになる高レジン含有バインダーの使用
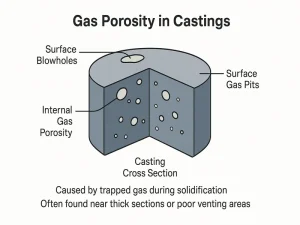
空気や水分の閉じ込めによる、金属鋳物の気孔や表面のブローホールの典型的な外観。
予防だ:
- 金型と中子を十分に乾燥させる。
- 低水素、高純度のチャージ材を使用する。
- 乱流を最小化するゲーティング設計の最適化
- 溶融処理中にアルゴンまたは窒素の脱ガスを行う
解決策
- 軽度の気孔は、溶接補修や含浸処理で対応できる。
- 持続的な問題に対しては、シミュレーションソフトウェアがガスの流れを可視化し、金型設計を改善するのに役立ちます。
収縮キャビティ
典型的な外観: 内部の空洞や陥没は、通常、厚い部分や効果的なライザー供給から遠い部分にある。これらは、しばしば大きな ダクタイル鋳鉄製ハウジングベアリング・ブロック、またはスチール・ベース・プレート。
👉 注:収縮空洞は、機械的強度と疲労寿命を著しく低下させる応力集中点につながる可能性があるため、構造用鋳物では特に問題となる。
原因がある:
収縮キャビティは、凝固の最終段階で、溶融金属がまだ収縮している領域に供給されないときに形成される。その要因には次のようなものがある:
- ライザーのサイズが小さい、または位置が悪い
- 凝固方向制御の欠如
- フィーダーネックの早期凍結
- 不均一な冷却速度の厚い断面
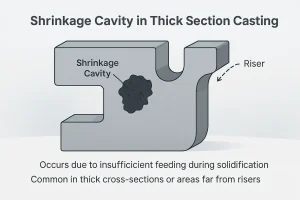
厚い部分の凝固による典型的な収縮空洞
予防だ:
- クリティカルゾーンに弾性率を合わせた適切なライザー設計
- 放熱を誘導するチルの使用
- ライザーの凝固を遅らせる断熱スリーブ
- トップダウン凝固を促進するために鋳造方向を調整する
解決策
- 鋳造形状の変更またはフィーダー量の増加
- アーク溶接または金属スプレーによる空洞補修(仕様で認められている場合)
コールド・シャット(ミスラン)
典型的な外観: 2つのメタル・フロントが融合しなかった接合部に見られる、薄く線状の不連続面または未融合の継ぎ目。多くの場合 薄肉鋳物複雑な形状や水平の継ぎ目。
👉 注:コールド・シャットは通常、表面に現れるが、重要なゾーンに内部クラックを形成し、シール面を損なったり、圧力下で早期破損を引き起こす可能性もある。
原因がある:
コールド・シャットは、部分的に凝固したメタル・フローが出会うが、そのために融合に至らない場合に発生する:
- 低い注湯温度
- 合金の流動性が悪い
- 長い流路や鋭角の金型設計
- コアやメタルチルによる高い熱損失
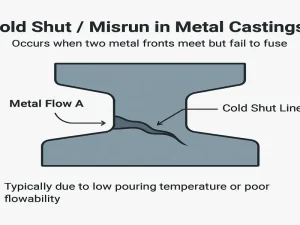
コールドシャット欠陥は、2つの溶融金属の前面が適切に融合せず、目に見える線や継ぎ目が残る場合に発生する。
予防だ:
- 合金固有の限界内で注湯温度を上げる
- ゲートをクリティカル・エリアに近づけることで、流れの長さを短くする。
- パターン・デザインに丸みを帯びたトランジションとフィレットを使う
- 流量を制限するようなサイズの小さい注入口は避ける。
解決策
- 速度ロスを減らすためにゲーティングシステムを変更
- 合金の選択を改善するか、流量を増加させる接種剤を使用する
- 構造の完全性が損なわれていなければ、局所的な修復は可能である。
介在物(スラグ/砂/酸化物)
典型的な外観: 機械加工された表面やNDT検査で見える、鋳物に埋め込まれた暗色または脆い粒子。これらは、スラグ、侵食された砂、酸化膜に由来する可能性がある。
👉 注:介在物は、機械加工や使用中に不具合が発生するまで隠れていることが多いため、早期発見が最も難しい欠陥のひとつである。
原因がある:
非金属介在物は様々な汚染源から発生する:
- メルトハンドリング中の不完全なスラグ除去
- 充填中の金型キャビティからの砂の浸食
- 金属の乱流による再酸化
- コア部分の緩み、または金型壁面のコーティング不足
予防だ:
- スラグ調整剤を使用し、取鍋のスキミングを徹底する。
- 注入口にセラミック・フォーム・フィルターを導入
- 金型強度と表面仕上げを一定に保つ
- 水しぶきと乱流を最小限に抑えるため、注ぐ高さを低くする。
解決策
- 表面の介在物は、機械加工によって除去することができる。
- 深い介在物は、特に重要な構造部品では不合格または再鋳造が必要。
- 冶金学的監査により、介在物の種類を特定の工程まで遡ることができる。
ホット・ティアーズ/サーマル・クラック
典型的な外観: ギザギザや枝分かれした亀裂で、通常、鋭角部、ボス部、肉厚の異なる接合部に発生する。これらの欠陥は、鋳物が内部の熱応力に対応できなくなる凝固の最終段階で形成される。
原因がある:
ホット・ティアーズは多くの場合、機械的拘束や金型の潰れにくさが原因である。主な要因は以下の通り:
- 肉厚の急激な変化
- 崩壊性の低い硬質砂型
- 高い注湯温度による広い凝固間隔
- 設計上の不十分なフィレットや応力緩和機能
予防だ:
- 均一な肉厚と滑らかな幾何学的変化
- 改良された金型材料または崩壊性を高める添加剤
- 注湯温度と鋳型予熱の制御
- リリーフノッチとフレキシブルコアを含む
解決策
- 軽微な亀裂は溶接で補修できる(仕様上可能な場合)
- 長期的な修正には通常、幾何学的な再設計または代替成形材料が必要である。
モールドシフト/コア変位
典型的な外観: 鋳物の異なる半分の間に段差や寸法のずれが生じ、肉厚が一定しなかったり、穴の位置がずれたりすること。
原因がある:
モールドシフトは、コープとドラッグの間のミスアライメント、または内部コアの移動によって引き起こされる。これは次のような原因で発生する:
- クランプ力不足またはフラスコへのはめ込みが緩い
- パターン摩耗または損傷したダボピン
- 注湯時の高い金属静圧または揺れ
予防だ:
- フラスコ固定具を強化し、正確な金型見当を確保する。
- 摩耗したパターン機器とコアプリントの交換
- 注湯の高さを調節して金属圧力を下げる
解決策
- 公差が許せば機械加工も可能である。
- パターン・ツーリングおよびアライメント・システムの再構築またはアップグレード
酸化膜/ドロス欠陥
典型的な外観: 鋳物表面の近くにある薄い膜状の層や脆い薄片で、機械加工中や金属組織分析中に初めて発見されることが多い。これらの介在物は耐疲労性を弱める。
原因がある:
酸化物関連の欠陥は、以下のような原因で形成される:
- 注湯中の溶融金属の酸素への暴露
- ゲーティングシステムの過度の乱気流
- 不適切な取鍋の取り扱いや遅延による再酸化
予防だ:
- 酸化を抑えるため、保護雰囲気(アルゴン)またはフラックスを使用する。
- 層流を可能にするゲート形状の最適化
- 注湯速度を制御することにより、金属の乱流を最小限に抑える。
解決策
- 表面酸化物は機械加工で除去できる場合もある。
- 深い内部酸化膜はリキャストとゲーティングの修正が必要
- 熱分析ツールは溶融実習の最適化に役立つ
不完全充填(アンダーフィル)
典型的な外観: 鋳物の欠落部、不完全なコーナー部、短い充填部、特に薄肉部品や表面積の大きい部品。
原因がある:
この欠陥は、溶融金属が凝固する前に金型キャビティを完全に満たさないために発生する。一般的な原因は以下の通り:
- 注湯温度が低い、または流動性が悪い
- 流れを制限したり、初期の乱流を誘発するゲートデザイン
- ガス抜き不良によるガスの背圧
- 複雑すぎる金型の特徴
予防だ:
- 合金限界内で注湯温度を上げる
- ゲート比と金型キャビティのエア抜けを改善
- 鋳造形状の簡素化、または複数部品設計への分割
- 真空アシスト技術を適用する
解決策
- 盛り土シミュレーションを評価し、問題のあるゾーンを特定する。
- フローとベント・システムを修正して再鋳造
鋳造欠陥の非破壊検査法
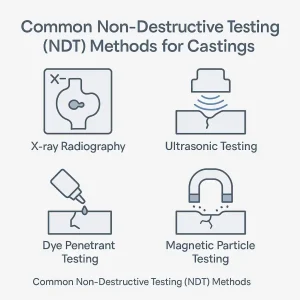
鋳物検査に使用される一般的な非破壊検査法:X線検査、超音波検査、染料浸透探傷検査、磁粉探傷検査。
試験方法 | 検出可能な欠陥 | 適した素材/用途 | 備考 |
---|---|---|---|
レントゲン撮影 | 内部収縮、ポロシティ、ボイド | 複雑な鋳物、肉厚部品 | 優れたディテール。 |
超音波検査 | サブサーフェイスクラック、インクルージョン | 大断面、スチール/ダクタイル鋳鉄 | オペレーターのスキルと良好なサーフェスが必要 |
染料浸透探傷検査 | 表面クラック、コールドシャット | 非多孔質金属(アルミニウム、スチール) | シンプルで手頃な価格。 |
磁性粒子 | 表面および表面近傍の欠陥 | 鉄(鋳鉄、鋼鉄) | 高速で信頼性が高い。 |
これらの試験方法は、機械加工または納入前に内部または外部の欠陥を特定するのに役立ち、鋳造部品が寸法および性能仕様に適合していることを保証します。
最終的な感想
鋳造の欠陥は、性能、コスト、顧客満足度に大きな影響を与えます。各欠陥の原因と是正策を明確に理解することで、鋳物工場もバイヤーも品質保証において積極的な役割を果たすことができます。
技術サポートや不具合解析をお探しですか? チームへのお問い合わせ 専門家のガイダンスとカスタム鋳造ソリューションのために。