Baja inversión en utillaje y plazos de entrega rápidos: Una ventaja estratégica
En el caso de los grandes componentes metálicos, los costes de utillaje y los plazos de entrega suelen ser factores decisivos para la viabilidad de un proyecto. La fundición en arena ofrece una clara ventaja en ambos frentes, sobre todo cuando la flexibilidad, la personalización y los ciclos de producción más cortos son fundamentales.
A diferencia de la fundición a presión o la fundición a la cera perdida, que requieren moldes de acero de alta precisión que pueden costar $20.000 o más, la fundición en arena utiliza moldes temporales hechos de arena y aglutinantes. La producción de estos moldes es mucho menos costosa y suelen prepararse en cuestión de días. Por ejemplo, la fundición en arena de la carcasa de una caja de cambios de un metro puede requerir una inversión en utillaje de sólo $2.000, casi una décima parte del coste de un molde metálico comparable.
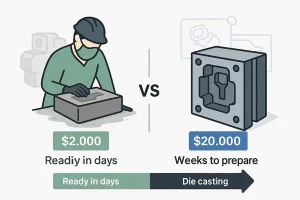
Comparación entre la rentabilidad de la fundición en arena y la velocidad de la fundición a presión
La velocidad es sólo una parte de la ecuación. Los moldes de arena pueden ajustarse fácilmente o reconstruidos para adaptarse a los cambios de diseño, lo que hace que el proceso sea ideal para pruebas de ingeniería, ingeniería inversa y fabricación de piezas bajo pedido. En sectores como el minero, el naval y el energético -donde los componentes de gran tamaño suelen requerir varias revisiones o sustituciones bajo demanda-, este nivel de flexibilidad reduce tanto el riesgo del proyecto como el desperdicio de capital.
Un molde permanente puede bloquear sus decisiones de diseño antes de tiempo. Un molde de arena le da libertad para evolucionar.
Ventajas a simple vista:
-
Menor inversión inicial para el desarrollo de moldes
-
Entrega rápida del CAD a la primera colada
-
Agilidad de diseño con revisiones o reconstrucciones de bajo coste
Si su plan de producción incluye lotes de tamaño medio, series piloto o iteraciones de diseño en fase avanzada, la fundición en arena le ofrece la eficacia de utillaje y la velocidad de respuesta que exigen los flujos de trabajo industriales modernos.
Libertad de diseño: Geometrías complejas a gran escala
Una de las ventajas más valiosas, aunque a menudo subestimada, del moldeo en arena es su excepcional flexibilidad de diseño, especialmente cuando se trata de componentes grandes y geométricamente complejos. A diferencia de los moldes metálicos permanentes, que imponen limitaciones estrictas en cuanto a forma, ángulo de inclinación y líneas de separación, los moldes de arena se forman a partir de patrones personalizados y pueden adaptarse para admitir prácticamente cualquier geometría.
La fundición en arena se adapta características internas como secciones huecas, nervaduras, resaltes y canales perforados transversalmente con núcleos de arena extraíbles.
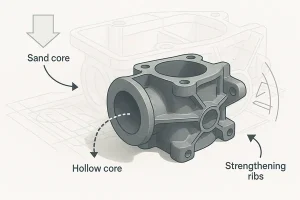
La fundición en arena permite obtener características complejas, como secciones huecas y nervaduras estructurales en componentes de gran tamaño.
Estas características pueden integrarse en una sola colada, eliminando la necesidad de soldadura, ensamblaje o múltiples pasos de fundición. Los ingenieros pueden optimizar el rendimiento estructural, reducir el peso y simplificar el mecanizado posterior, todo ello sin comprometer la fabricabilidad.
Esta capacidad es especialmente importante para componentes de gran tamaño en aplicaciones exigentes, como:
-
- Carcasas de bombas con vías de flujo integradas
-
- Bloques de motor con galerías de refrigeración internas
-
- Cubos de aerogeneradores con cavidades multiaxiales profundas
-
- Bastidores de maquinaria pesada con nervios de refuerzo empotrados
Dado que los moldes de arena son desechables, los cambios de diseño son fáciles y económicos de implementar. Ya se trate de cambiar la posición de un orificio para un tornillo, modificar el grosor de la pared o adaptar una brida, los ingenieros pueden realizar ajustes sin desechar costosas herramientas. Esta flexibilidad permite perfeccionar el diseño en las últimas fases, crear prototipos o iterar rápidamente durante los ciclos de desarrollo.
La geometría compleja no debe ser una limitación, sino una oportunidad de diseño.
En sectores en los que el tamaño y el rendimiento son tan importantes como la precisión, la fundición en arena permite a los ingenieros materializar plenamente su intención de diseño. Elimina las limitaciones impuestas por las herramientas rígidas y favorece la innovación a gran escala.
Compatible con aleaciones de alta temperatura como el acero y la fundición dúctil
La fundición en arena destaca donde muchos otros métodos fracasan: en la manipulación de metales de alto punto de fusión como el acero al carbono, el acero aleado y la fundición dúctil. Estos materiales son esenciales para aplicaciones pesadas que exigen solidez, resistencia al calor y una larga vida útil, pero plantean serios retos para los procesos de fundición que se basan en moldes permanentes.
La fundición a presión, por ejemplo, está optimizada para aleaciones de bajo punto de fusión como el aluminio, el magnesio o el zinc. Sus moldes de acero simplemente no pueden soportar las temperaturas extremas -a menudo superiores a 1500°C (2730°F)- necesarias para verter acero o hierro fundidos.
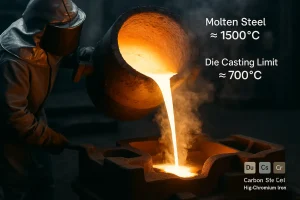
Vertido de metal fundido en un molde de arena, adecuado para aleaciones de alta temperatura como la fundición dúctil y el acero.
Incluso con sistemas de refrigeración, la fatiga térmica del utillaje hace que la fundición a presión sea técnica y económicamente inviable para estos metales.
La fundición en arena evita por completo este problema. Al utilizar arena de sílice o cromita resistente al calor, los moldes son totalmente desechables y no se ven afectados por las temperaturas del metal fundido. Esto hace que el proceso sea ideal para la fundición de aleaciones ferrosas, incluidas:
-
- Hierro dúctil para carcasas de cajas de cambios y brazos de suspensión
-
- Acero de baja aleación para cubos de aerogeneradores y bastidores de transmisión
-
- Planchas de alto contenido en cromo para revestimientos resistentes al desgaste en equipos de minería y trituración
Debido a esta compatibilidad, la fundición en arena es la opción por defecto para componentes estructurales y de soporte de presión en industrias como la generación de energía, la maquinaria todoterreno y la ingeniería naval.
No se elige el moldeo en arena sólo por la geometría, sino cuando el propio metal lo exige.
Cuando su proyecto requiere un rendimiento robusto en condiciones de gran tensión o calor, el moldeo en arena proporciona la flexibilidad de material que otros métodos simplemente no pueden ofrecer.
Superar los defectos: Cómo garantiza la calidad la fundición en arena moderna
Históricamente, la fundición en arena ha estado asociada a la rugosidad superficial, la variabilidad dimensional y los defectos internos. Pero en las fundiciones modernas, estos problemas ya no son inherentes al proceso, sino problemas de ingeniería con soluciones conocidas y controladas.
Los flujos de trabajo de fundición actuales incorporan Simulación de solidificación basada en CAE, sistemas de moldeo automatizadosy ensayos no destructivos (END) para garantizar la calidad de las piezas desde el diseño hasta la inspección final. El resultado: piezas de fundición en arena que cumplen sistemáticamente las exigentes especificaciones industriales.
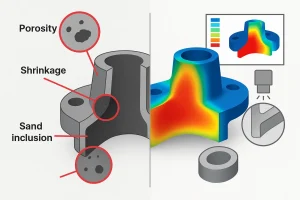
Visualización en paralelo de la fundición en arena tradicional por ensayo y error frente a la simulación moderna para una mayor precisión.
Defectos comunes y soluciones modernas:
-
- Porosidad y contracción
Eliminación mediante modelado de solidificación en 3D, optimización del tubo ascendente y curvas de enfriamiento controladas.
- Porosidad y contracción
-
- Inclusión de arena
Se evita mediante un diseño adecuado de las compuertas, sistemas de filtración y procedimientos de limpieza del moho.
- Inclusión de arena
-
- Distorsión o deformación
Reducción gracias a la compactación uniforme del molde y a la aplicación uniforme de aglutinante
- Distorsión o deformación
Al simular el flujo de calor y la solidificación del metal antes de la primera colada, los ingenieros pueden identificar las zonas de riesgo, como los puntos calientes, y garantizar una geometría del molde y una ventilación óptimas. Este enfoque proactivo reduce drásticamente las tasas de defectos, especialmente en componentes grandes y de gran masa.
Ejemplo de aplicación:
En un reciente proyecto de carcasas de cajas de engranajes para equipos de minería, la simulación reveló un riesgo de contracción en las intersecciones de las bridas de los pernos. Los ingenieros cambiaron la posición de las bandas y ajustaron las vías de refrigeración. El resultado: éxito a la primera, verificado por inspección ultrasónica (UT), sin necesidad de retrabajo.
Conclusión:
La fundición en arena moderna es de calidad y proceso controlado. Con herramientas digitales, diagnósticos avanzados e inspección rigurosa (ultrasónica, radiográfica y por penetración de colorante), ofrece un rendimiento constante para piezas críticas en sectores como la generación de energía, la construcción y el transporte.
Cuando la precisión se une a la disciplina del proceso, la fundición en arena se convierte en una solución fiable, no en un compromiso.
Cuándo elegir el moldeo en arena en lugar de otros métodos
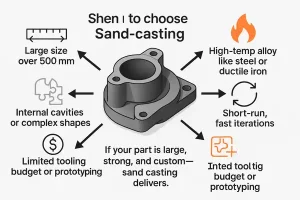
Guía visual para la selección de fundición en arena para componentes grandes, personalizados y de alta temperatura.
Con una amplia gama de tecnologías de fundición disponibles -fundición en coquilla, fundición a la cera perdida, molde permanente- es importante saber cuándo la fundición en arena es la más adecuada. La elección depende de varios factores clave: tamaño de la pieza, geometría, aleación, cantidad y flexibilidad de diseño.
La fundición en arena es su mejor opción cuando:
-
La pieza es grande (normalmente más de 10 kg o 500 mm de tamaño)
-
El material es una aleación de alta temperatura, como el acero o la fundición dúctil.
-
El diseño incluye características internas complejas, nervaduras o cavidades
-
Necesita producción en tiradas cortas, creación rápida de prototipos o recambios de posventa
-
Se esperan cambios de diseño o personalización en las últimas fases
Por el contrario, fundición a presión es ideal para componentes pequeños y medianos de aluminio o zinc producidos en volúmenes muy elevados con una tolerancia dimensional ajustada. Fundición a la cera perdida es el mejor para piezas pequeñas y complejas que requieren un excelente acabado superficial, pero conlleva un mayor coste por unidad y más tiempo de mecanizado.
La fundición en arena no es sólo un remedio: es un proceso estratégico para el tamaño, la complejidad y la adaptabilidad.
Nota final:
Si su proyecto exige resistencia estructural, flexibilidad de ingeniería y eficiencia económica -sin comprometerse a fabricar grandes volúmenes de herramientas-, la fundición en arena es la solución que se ajusta a las necesidades industriales del mundo real.
Descubra nuestras capacidades de fundición en arena o póngase en contacto con nosotros para solicitar un presupuesto. Le ayudaremos a evaluar la viabilidad y optimizar el rendimiento.