1. Why Aluminum Casting Tolerances Matter
Scene Introduction:
Designer asks, “Can we make this housing with a ±0.1 mm tolerance?”
Engineer replies, “That depends on the casting process you choose—and whether there’s any post-machining.”
Dimensional tolerances directly influence part fit, sealing ability, and assembly accuracy. Unlike iron or steel, aluminum has higher thermal expansion and tends to deform more easily during solidification and cooling.
- 🎯 Key Points
- Aluminum castings vary more than ferrous parts due to alloy behavior.
- Not all tolerances need to be tight—design with function in mind.
- Understanding the process–tolerance–cost relationship is critical.
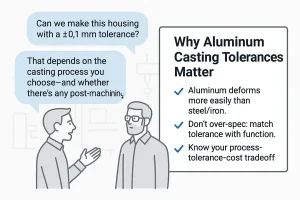
Why aluminum casting tolerances impact fit, sealing, and precision.
2. Typical Tolerances by Casting Process
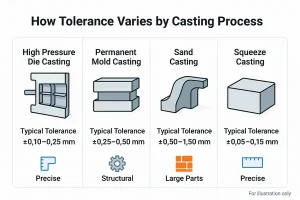
Typical tolerance ranges across different aluminum casting processes: HPDC, sand casting, permanent mold, and squeeze casting.
Casting Process | Typical Tolerance | Achievable Range | Notes |
---|---|---|---|
High Pressure Die Cast | ±0.10–0.25 mm | ±0.10 mm | Best for thin walls, precision parts |
Permanent Mold Casting | ±0.25–0.50 mm | ±0.15 mm | Good repeatability, moderate cost |
Sand Casting | ±0.8–1.5 mm | ±0.5 mm | Suitable for large or simple parts |
Squeeze Casting | ±0.05–0.15 mm | ±0.05 mm | Structural, high-strength components |
✅ Pro Tip: It’s often better to “cast first, machine later” when tight tolerances are needed.
3. Aluminum Casting Standards You Should Know
ISO 8062: Defines Casting Tolerance Grades (CT1–CT12). For aluminum:
- CT6: Tight (±0.3 mm)
- CT7–CT8: Typical applications
- CT11: Rough sand casting
NADCA #207: Targeted at die casting; more specific than ISO for smaller parts.
⚠️ Common Pitfall: Blindly selecting CT grades without considering aluminum shrinkage and mold setup can lead to problems.
4. What Affects Final Tolerance?
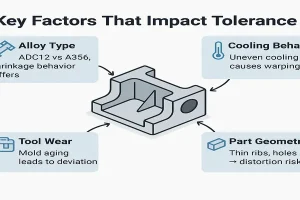
Key factors that influence dimensional stability in aluminum casting processes.
- Alloy Type: Different aluminum grades (e.g., ADC12 vs A356) have different shrinkage rates.
- Cooling Behavior: Uneven cooling can cause warping and distortion.
- Tool Wear & Setup: Mold wear or poor alignment leads to gradual tolerance drift.
- Part Geometry: Thin ribs, holes, and unsupported sections are harder to control.
🧠 Insight: “Complex geometry = high-risk dimension.”
5. Tolerance vs Cost: Where Is the Jump?
“I want ±0.1 mm, but I can’t increase the budget.”
Tighter tolerances often mean more expensive tooling or added machining—expect 20–50% more cost per step.
Smart approach: use casting for bulk shape, machine only the critical zones.
6. Can You Really Cast ±0.1 mm?
Yes, if:
- You use high-pressure die casting (HPDC) or squeeze casting
- The mold is high-precision with controlled cooling
- Critical surfaces are machined afterward
No, if:
- You’re using sand casting
- Wall thickness is thin or asymmetric
- You expect precision from casting alone on sealing surfaces
✅ Pro Tip: ±0.1 mm is achievable—but don’t expect to get it without machining.
7. Design Guidelines for Better Tolerances
- Use draft angles ≥ 1°
- Keep wall thickness consistent
- Add 1.0–1.5 mm machining allowance
- Avoid unsupported ribs or thin walls
💡 Design Insight: “Precision starts with allowing room for machining.”
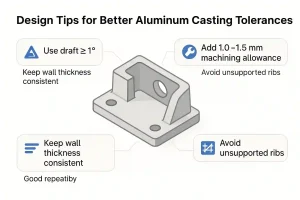
Tips for improving aluminum casting accuracy through smart design.
8. Post-Casting Adjustments
- CNC Machining: Achieves ±0.01–0.05 mm
- Heat Treatment: May induce warping—tolerances should be re-verified
- Surface Finishing: Anodizing adds 5–25 μm layer
9. Final Decision Table
Feature | Suggested Tolerance | Process | Machining Required | Cost Level |
---|---|---|---|---|
Hole Ø10–20 mm | ±0.10 mm | HPDC | Yes | ★★★ |
Flat surface 100×100 mm | ±0.25 mm | Permanent Mold | No | ★★ |
Length >300 mm | ±1.00 mm | Sand Casting | No | ★ |
10. Conclusion & Call to Action
Aluminum casting tolerances are all about balance—tight enough to function, loose enough to manufacture efficiently.
“Tight enough to work, loose enough to cast.”
Need aluminum castings with precision you can trust? Contact us today →