Baixo investimento em ferramentas e rapidez de execução: Uma vantagem estratégica
Para grandes componentes metálicos, os custos de ferramentas e os prazos de entrega são muitas vezes factores decisivos para a viabilidade de um projeto. A fundição em areia oferece uma clara vantagem em ambas as frentes - particularmente quando a flexibilidade, a personalização e os ciclos de produção mais curtos são críticos.
Ao contrário da fundição sob pressão ou da fundição de investimento, que requerem moldes de aço de alta precisão que podem custar $20.000 ou mais, a fundição em areia utiliza moldes temporários feitos de areia e aglutinantes. A produção destes moldes é muito menos dispendiosa e, normalmente, podem ser preparados numa questão de dias. Por exemplo, a fundição em areia de uma caixa de velocidades de 1 metro pode exigir um investimento em ferramentas de apenas $2.000 - quase um décimo do custo de um molde de metal comparável.
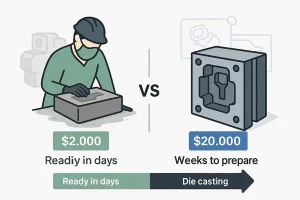
Uma imagem lado a lado que mostra a relação custo-eficácia da fundição em areia versus a vantagem da velocidade da fundição sob pressão
A velocidade é apenas uma parte da equação. Os moldes de areia podem ser facilmente ajustados ou reconstruídos para acomodar alterações de design, tornando o processo ideal para ensaios de engenharia, engenharia inversa e peças feitas por encomenda. Em indústrias como a mineira, marítima e energética - onde os grandes componentes requerem frequentemente múltiplas revisões ou substituição a pedido - este nível de flexibilidade reduz o risco do projeto e o desperdício de capital.
Um molde permanente pode bloquear precocemente as suas decisões de design. Um molde em areia dá-lhe a liberdade de evoluir.
Benefícios num relance:
-
Menor investimento inicial para o desenvolvimento de moldes
-
Rápida execução do CAD ao primeiro vazamento
-
Agilidade de conceção com revisões ou reconstruções de baixo custo
Se o seu plano de produção inclui lotes de tamanho médio, execuções-piloto ou iterações de design em fase tardia, a fundição em areia proporciona a eficiência das ferramentas e a velocidade de resposta que os fluxos de trabalho industriais modernos exigem.
Liberdade de design: Suporte de geometrias complexas e de grande escala
Uma das vantagens mais valiosas, mas frequentemente subestimadas, da fundição em areia é a sua excecional flexibilidade de conceção - especialmente quando se trata de componentes grandes e geometricamente complexos. Ao contrário dos moldes metálicos permanentes, que impõem limitações rigorosas em termos de forma, ângulo de inclinação e linhas de separação, os moldes em areia são formados em torno de padrões personalizados e podem ser adaptados para suportar praticamente qualquer geometria.
A fundição em areia acomoda caraterísticas internas tais como secções ocas, nervuras, saliências e canais perfurados transversalmente utilizando núcleos de areia amovíveis.
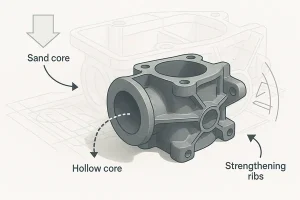
A fundição em areia permite caraterísticas complexas como secções ocas e nervuras estruturais em componentes de grandes dimensões
Estas caraterísticas podem ser integradas num único vazamento, eliminando a necessidade de soldadura, montagem ou múltiplos passos de fundição. Os engenheiros podem otimizar o desempenho estrutural, reduzir o peso e simplificar a maquinação a jusante - tudo isto sem comprometer a capacidade de fabrico.
Esta capacidade é especialmente importante para componentes de grandes dimensões em aplicações exigentes, tais como:
-
- Caixas de bombas com vias de escoamento integradas
-
- Blocos de motor com galerias de refrigeração internas
-
- Cubos de turbinas eólicas com cavidades profundas multi-eixo
-
- Estruturas para máquinas pesadas com nervuras de reforço incorporadas
Uma vez que os moldes de areia são descartáveis, as alterações de design são fáceis e económicas de implementar. Quer se trate de reposicionar um orifício de parafuso, alterar a espessura da parede ou adaptar uma flange, os engenheiros podem efetuar ajustes sem descartar ferramentas dispendiosas. Esta flexibilidade permite o refinamento da fase final do projeto, a criação de protótipos ou a iteração rápida durante os ciclos de desenvolvimento.
A geometria complexa não deve ser uma restrição - deve ser uma oportunidade de design.
Nas indústrias em que o tamanho e o desempenho são tão importantes como a precisão, a fundição em areia permite que os engenheiros realizem plenamente a intenção do seu projeto. Elimina as restrições impostas por ferramentas rígidas e apoia a inovação à escala.
Compatível com ligas de alta temperatura, como aço e ferro dúctil
A fundição em areia destaca-se onde muitos outros métodos falham: no manuseamento de metais com elevado ponto de fusão, como o aço-carbono, o aço-liga e o ferro dúctil. Estes materiais são essenciais para aplicações pesadas que exigem força, resistência ao calor e longa vida útil - mas colocam sérios desafios aos processos de fundição que dependem de moldes permanentes.
A fundição sob pressão, por exemplo, é optimizada para ligas de baixo ponto de fusão, como o alumínio, o magnésio ou o zinco. Os seus moldes de aço simplesmente não conseguem suportar as temperaturas extremas - muitas vezes superiores a 1500°C (2730°F) - necessárias para verter aço ou ferro fundido.
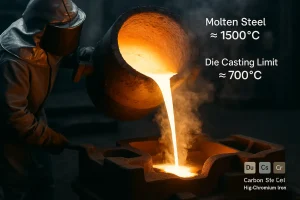
Metal fundido a ser vertido para um molde de areia, adequado para ligas de alta temperatura como o ferro dúctil e o aço
Mesmo com sistemas de arrefecimento, a fadiga térmica nas ferramentas torna a fundição injetada técnica e economicamente impraticável para estes metais.
A fundição em areia evita totalmente este problema. Utilizando areia de sílica ou cromite resistente ao calor, os moldes são totalmente descartáveis e não são afectados pelas temperaturas do metal fundido. Este facto torna o processo ideal para a fundição de ligas ferrosas, incluindo:
-
- Ferro fundido dúctil para caixas de velocidades e braços de suspensão
-
- Aço de baixa liga para cubos de turbinas eólicas e estruturas de transmissão
-
- Ferros com alto teor de crómio para revestimentos resistentes ao desgaste em equipamento mineiro e de britagem
Devido a esta compatibilidade, a fundição em areia é a escolha padrão para componentes estruturais e de suporte de pressão em indústrias como a geração de energia, maquinaria fora de estrada e engenharia marítima.
Não se escolhe a fundição em areia apenas pela geometria - escolhe-se quando o próprio metal o exige.
Quando o seu projeto exige um desempenho robusto em condições de elevada tensão ou de elevado calor, a fundição em areia proporciona a flexibilidade do material que outros métodos simplesmente não conseguem suportar.
Superar os defeitos: Como a fundição em areia moderna garante a qualidade
A fundição em areia tem sido historicamente associada à rugosidade da superfície, variabilidade dimensional e defeitos internos. Mas nas fundições modernas, estas questões já não são inerentes ao processo - são problemas de engenharia com soluções conhecidas e controladas.
Os actuais fluxos de trabalho de casting incorporam Simulação de solidificação baseada em CAE, sistemas de moldagem automatizadose ensaios não destrutivos (NDT) para garantir a qualidade das peças, desde o modelo até à inspeção final. O resultado: peças fundidas em areia que cumprem consistentemente as exigentes especificações industriais.
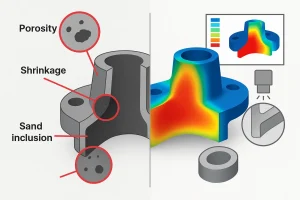
Imagem lado a lado mostrando a tradicional fundição em areia por tentativa e erro versus a moderna simulação para uma melhor precisão
Defeitos comuns e soluções modernas:
-
- Porosidade e retração
Eliminado através da utilização de modelação de solidificação 3D, otimização de risers e curvas de arrefecimento controladas
- Porosidade e retração
-
- Inclusão de areia
Prevenido através de uma conceção adequada das comportas, sistemas de filtragem e procedimentos de limpeza dos moldes
- Inclusão de areia
-
- Distorção ou deformação
Reduzido pela compactação uniforme do molde e aplicação consistente de ligante
- Distorção ou deformação
Ao simular o fluxo de calor e a solidificação do metal antes do primeiro vazamento, os engenheiros podem identificar áreas de risco, como pontos quentes, e garantir a geometria e a ventilação ideais do molde. Esta abordagem proactiva reduz drasticamente as taxas de defeitos - especialmente em componentes grandes e de elevada massa.
Exemplo de aplicação:
Num projeto recente de alojamento de caixa de velocidades para equipamento mineiro, a simulação revelou um risco de retração nas intersecções das flanges dos parafusos. Os engenheiros reposicionaram os risers e ajustaram os caminhos de arrefecimento. O resultado: sucesso à primeira tentativa, verificado por inspeção ultra-sónica (UT), sem necessidade de retrabalho.
Conclusão:
A fundição em areia moderna é com capacidade para a qualidade e controlado por processos. Com ferramentas digitais, diagnósticos avançados e uma inspeção rigorosa - ultra-sónica, radiográfica e por penetração de corante - proporciona um desempenho consistente para peças críticas em indústrias como a produção de energia, a construção e os transportes.
Quando a precisão se alia à disciplina do processo, a fundição em areia torna-se uma solução fiável - não um compromisso.
Quando escolher a fundição em areia em vez de outros métodos
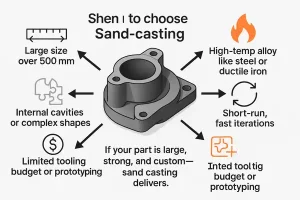
Guia visual para a seleção de fundição em areia para componentes grandes, personalizados e de alta temperatura.
Com uma vasta gama de tecnologias de fundição disponíveis - fundição sob pressão, fundição de investimento, molde permanente - é importante saber quando é que a fundição em areia é a melhor opção. A escolha depende de vários factores-chave: tamanho da peça, geometria, liga, quantidade e flexibilidade do design.
A fundição em areia é a sua melhor opção quando:
-
A peça é grande (normalmente mais de 10 kg ou 500 mm de tamanho)
-
O material é uma liga de alta temperatura como o aço ou o ferro dúctil
-
O desenho inclui caraterísticas internas complexas, nervuras ou cavidades
-
Necessita de produção de pequenas tiragens, prototipagem rápida ou substituições no mercado pós-venda
-
São esperadas alterações ou personalizações na fase final do projeto
Em contrapartida, fundição injectada é ideal para componentes pequenos a médios de alumínio ou zinco produzidos em volumes muito elevados com tolerância dimensional apertada. Fundição por cera perdida é a melhor opção para peças pequenas e complexas que requerem um excelente acabamento superficial - mas tem um custo unitário mais elevado e um maior tempo de utilização das ferramentas.
A fundição em areia não é apenas um recurso - é um processo estratégico para tamanho, complexidade e adaptabilidade.
Nota final:
Se o seu projeto exige resistência estrutural, flexibilidade de engenharia e eficiência económica - sem se comprometer com ferramentas de grande volume - a fundição em areia é a solução que se alinha com as necessidades industriais do mundo real.
Explore as nossas capacidades de fundição em areia ou entrar em contacto para um orçamento. Ajudamo-lo a avaliar a viabilidade e a otimizar o desempenho.