Compreender os defeitos de fundição na prática de fundição
Os defeitos de fundição são falhas ou irregularidades que ocorrem durante o processo de fundição, comprometendo potencialmente a integridade estrutural, a exatidão dimensional ou o aspeto do produto final. Nas indústrias que dependem de componentes de alto desempenho - como a automóvel, a construção ou a hidráulica - compreender como e porquê surgem estes defeitos é fundamental para produtores e compradores.
Este guia descreve os defeitos de fundição mais frequentes encontrados em fundições de ferro dúctil, ferro cinzento e aço. Para cada um deles, abordamos indicadores visuais típicos, causas subjacentes, estratégias preventivas e possíveis soluções.
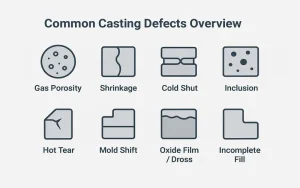
Panorâmica visual de oito tipos comuns de defeitos de fundição ilustrados com ícones e etiquetas.
Porosidade do gás
Aspeto típico: Pequenas cavidades arredondadas ou vazios, quer na superfície quer embutidos na peça fundida. Estes são especialmente problemáticos em componentes de retenção de pressão como caixas de bombas ou corpos de válvulas.
👉 Nota: Os estudos da indústria indicam que a porosidade do gás e a contração em conjunto representam até 50% de todos os defeitos de fundição, tornando-os os tipos mais comuns e críticos a monitorizar.
Causas:
A porosidade gasosa em peças fundidas de ferro fundido dúctil e aço resulta tipicamente do aprisionamento de gás durante a solidificação. Isto pode ser causado por:
- Humidade excessiva no molde ou nos materiais do núcleo
- Desgaseificação incompleta do metal fundido
- Má ventilação do molde ou turbulência excessiva durante o vazamento
- Utilização de aglutinantes com elevado teor de resina que se decompõem em gás
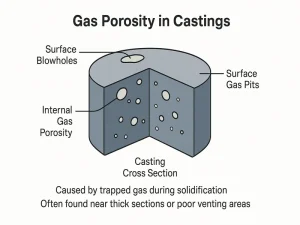
Aspeto típico da porosidade do gás e das bolhas superficiais em peças fundidas de metal devido ao ar ou à humidade retidos.
Prevenção:
- Assegurar que os moldes e os núcleos estão completamente secos
- Utilizar materiais de carga com baixo teor de hidrogénio e de elevada pureza
- Otimizar a conceção das comportas para minimizar a turbulência
- Utilizar a desgaseificação com árgon ou azoto durante o tratamento da fusão
Soluções:
- As porosidades menores podem ser resolvidas através de reparação de soldaduras ou impregnação
- Para problemas persistentes, o software de simulação pode ajudar a visualizar o fluxo de gás e melhorar o design do molde
Cavidades de retração
Aspeto típico: Vazios internos ou áreas afundadas normalmente localizadas em secções mais espessas ou áreas distantes da alimentação efectiva do riser. Estes ocorrem frequentemente em grandes caixas de ferro fundido dúctil, blocos de rolamentos ou placas de base em aço.
👉 Nota: As cavidades de contração são particularmente problemáticas em peças fundidas estruturais, uma vez que podem conduzir a pontos de concentração de tensões que reduzem significativamente a resistência mecânica e a vida à fadiga.
Causas:
As cavidades de contração formam-se durante a fase final da solidificação, quando o metal fundido não consegue alimentar as regiões que ainda se estão a contrair. Os factores que contribuem para isso incluem:
- Elevadores subdimensionados ou mal posicionados
- Falta de controlo da solidificação direcional
- Congelamento prematuro dos pescoços dos comedouros
- Secções transversais espessas com taxas de arrefecimento irregulares
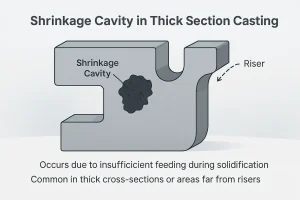
Uma cavidade de retração típica causada pela solidificação em secções espessas
Prevenção:
- Conceção adequada do riser com correspondência do módulo às zonas críticas
- Utilização de arrefecimentos para orientar a dissipação de calor
- Mangas isolantes para retardar a solidificação da coluna
- Ajustar a orientação da fundição para promover a solidificação de cima para baixo
Soluções:
- Modificar a geometria da fundição ou aumentar o volume do alimentador
- Reparar cavidades utilizando soldadura por arco ou pulverização de metal (quando permitido pelas especificações)
Calado a frio (Misrun)
Aspeto típico: Descontinuidades finas e lineares ou costuras não fundidas em junções onde duas frentes metálicas não se fundiram. Frequentemente observadas em peças fundidas de paredes finasA utilização de um sistema de proteção contra a corrosão é feita através de uma rede de proteção contra a corrosão, de geometrias complexas ou de juntas horizontais.
👉 Nota: Embora as juntas frias sejam normalmente visíveis à superfície, podem também formar fissuras internas em zonas críticas, comprometendo potencialmente as superfícies de vedação ou causando uma falha prematura sob pressão.
Causas:
O corte a frio ocorre quando fluxos de metal parcialmente solidificados se encontram mas não se fundem devido a:
- Baixas temperaturas de vazamento
- Fraca fluidez da liga
- Caminhos de fluxo longos ou cantos afiados na conceção do molde
- Elevada perda de calor através dos núcleos ou dos arrefecimentos metálicos
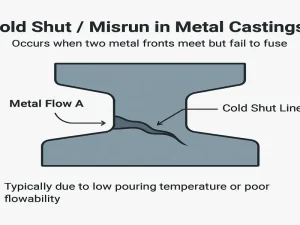
O defeito de corte a frio ocorre quando duas frentes de metal fundido não se fundem corretamente, deixando uma linha ou costura visível.
Prevenção:
- Aumentar a temperatura de vazamento dentro dos limites específicos da liga
- Reduzir o comprimento do caudal deslocando as comportas para mais perto das zonas críticas
- Utilizar transições arredondadas e filetes na conceção de padrões
- Evitar entradas subdimensionadas que limitem o caudal
Soluções:
- Modificar o sistema de comportas para reduzir a perda de velocidade
- Melhorar a seleção de ligas ou utilizar inoculantes que aumentem o fluxo
- Se a integridade estrutural não estiver comprometida, poderá ser possível uma reparação localizada
Inclusões (escória / areia / óxidos)
Aspeto típico: Partículas escuras ou quebradiças incorporadas na peça fundida, visíveis nas superfícies maquinadas ou através de inspeção NDT. Estas podem ter origem em escórias, areia erodida ou películas de óxido.
👉 Nota: As inclusões estão entre os defeitos mais difíceis de detetar precocemente, uma vez que muitas vezes permanecem ocultas até ocorrer uma falha na maquinagem ou em serviço - especialmente em aplicações de alta pressão ou sensíveis à fadiga.
Causas:
As inclusões não metálicas resultam de várias fontes de contaminação:
- Remoção incompleta de escórias durante o manuseamento da massa fundida
- Erosão de areia da cavidade do molde durante o enchimento
- Reoxidação causada pela turbulência dos metais
- Secções do núcleo soltas ou revestimento insuficiente nas paredes do molde
Prevenção:
- Utilizar acondicionadores de escórias e efetuar uma escumação completa da concha
- Introduzir filtros de espuma de cerâmica nas entradas
- Manter a resistência do molde e o acabamento da superfície consistentes
- Reduzir a altura de vazamento para minimizar os salpicos e a turbulência
Soluções:
- As inclusões superficiais podem ser removidas por maquinagem
- As inclusões profundas requerem a rejeição ou a fundição de novo, especialmente em peças estruturais críticas
- As auditorias metalúrgicas podem rastrear os tipos de inclusão até etapas específicas do processo
Lágrimas quentes / Fissuras térmicas
Aspeto típico: Fissuras recortadas ou ramificadas, que ocorrem normalmente em cantos agudos, saliências ou junções de espessura de parede variável. Estes defeitos formam-se durante as fases finais da solidificação, quando a peça fundida não consegue acomodar as tensões térmicas internas.
Causas:
As rupturas a quente são frequentemente o resultado de uma restrição mecânica ou de uma fraca colapsabilidade do molde. Os principais factores que contribuem para isso incluem:
- Alterações abruptas da espessura da parede
- Moldes de areia rígida com baixa colapsabilidade
- Altas temperaturas de vazamento causando grandes intervalos de solidificação
- Filetes ou elementos de alívio de tensões inadequados na conceção
Prevenção:
- Espessura uniforme da parede e transições geométricas suaves
- Materiais de molde melhorados ou aditivos que aumentam a colapsibilidade
- Controlo da temperatura de vazamento e do pré-aquecimento do molde
- Inclusão de entalhes em relevo e núcleos flexíveis
Soluções:
- As fissuras menores podem ser reparadas por soldadura (se as especificações o permitirem)
- A correção a longo prazo envolve normalmente uma nova conceção geométrica ou materiais de moldagem alternativos
Deslocação do molde / Deslocação do núcleo
Aspeto típico: Superfícies escalonadas ou desalinhamento dimensional entre diferentes metades da peça fundida, resultando em espessuras de parede inconsistentes ou furos deslocados.
Causas:
O deslocamento do molde é causado pelo desalinhamento entre o cope e o arrasto, ou pelo movimento dos núcleos internos. Isto pode ocorrer devido a:
- Força de aperto inadequada ou ajuste frouxo do frasco
- Desgaste do padrão ou cavilhas danificadas
- Elevada pressão metalostática ou vibração durante o vazamento
Prevenção:
- Reforçar as fixações dos frascos e assegurar um registo preciso do molde
- Substituir o equipamento de modelação e as impressões centrais desgastados
- Ajuste a altura de vazamento para reduzir a pressão do metal
Soluções:
- A maquinagem pode ser possível se as tolerâncias o permitirem
- Reconstrução ou atualização de ferramentas de modelação e sistemas de alinhamento
Filmes de óxido / Defeitos de escória
Aspeto típico: Camadas finas, semelhantes a películas ou flocos frágeis perto da superfície da peça fundida, muitas vezes só descobertas durante a maquinagem ou em análises metalográficas. Estas inclusões enfraquecem a resistência à fadiga.
Causas:
Os defeitos relacionados com o óxido formam-se devido a:
- Exposição do metal fundido ao oxigénio durante o vazamento
- Turbulência excessiva no sistema de gating
- Reoxidação causada por manuseamento incorreto da concha ou atraso
Prevenção:
- Utilizar uma atmosfera protetora (árgon) ou um fluxo para reduzir a oxidação
- Otimizar a geometria da porta para permitir um fluxo laminar
- Minimizar a turbulência do metal através do controlo da velocidade de vazamento
Soluções:
- O óxido de superfície pode, por vezes, ser removido por maquinagem
- Os óxidos internos profundos requerem uma revisão da fundição e da gutação
- As ferramentas de análise térmica podem ajudar a otimizar a prática da fusão
Enchimento incompleto (enchimento insuficiente)
Aspeto típico: Secções em falta, cantos incompletos ou preenchimentos curtos em peças fundidas - especialmente em peças de paredes finas ou de grande superfície.
Causas:
Este defeito é causado pelo facto de o metal fundido não preencher completamente a cavidade do molde antes de solidificar. As razões mais comuns incluem:
- Baixa temperatura de vazamento ou fraca fluidez
- Conceção de comportas que restringe o fluxo ou induz turbulência precoce
- Contrapressão de gás devido a ventilação deficiente
- Caraterísticas do molde demasiado complexas
Prevenção:
- Aumentar a temperatura de vazamento dentro dos limites da liga
- Melhorar o rácio de fecho e a saída de ar da cavidade do molde
- Simplificar a geometria da fundição ou dividi-la em desenhos de várias partes
- Aplicar técnicas de assistência ao vácuo, se for caso disso
Soluções:
- Avaliar as simulações de enchimento para localizar as zonas problemáticas
- Reformulação com sistemas de fluxo e ventilação corrigidos
Métodos de ensaio não destrutivos para defeitos de fundição
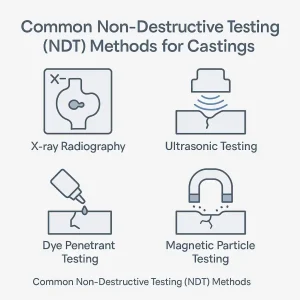
Métodos NDT comuns utilizados para a inspeção de peças fundidas: Ensaios de raios X, ultra-sons, penetração de corante e partículas magnéticas.
Método de ensaio | Defeitos detectáveis | Materiais Adequados / Utilizações | Notas |
---|---|---|---|
Radiografia de raios X | Contração interna, porosidade, vazios | Peças fundidas complexas, peças de paredes espessas | Excelente pormenor; mais caro |
Ensaios por ultra-sons | Fissuras subsuperficiais, inclusões | Grandes secções, aço/ferro fundido | Requer habilidade do operador e boa superfície |
Teste de Penetrante de Corante | Fissuras na superfície, fechos frios | Metais não porosos (alumínio, aço) | Simples, acessível; apenas visível à superfície |
Partícula magnética | Defeitos à superfície e próximos da superfície | Metais ferrosos (ferro fundido, aço) | Rápido e fiável; limitado a peças magnéticas |
Estes métodos de ensaio ajudam a identificar defeitos internos ou externos antes da maquinagem ou da entrega, garantindo que os seus componentes fundidos cumprem as especificações dimensionais e de desempenho.
Considerações finais
Os defeitos de fundição podem afetar significativamente o desempenho, o custo e a satisfação do cliente. Com uma compreensão clara das causas de cada defeito e das estratégias de correção, tanto as fundições como os compradores podem assumir um papel proactivo na garantia da qualidade.
Procura apoio técnico ou análise de defeitos? Contactar a nossa equipa para obter orientação especializada e soluções de fundição personalizadas.