Understanding Cast Iron: Structure and Importance
Cast iron has long stood as a pillar of industrial manufacturing. But why is it still relevant in an age of advanced alloys and composites? From ancient Chinese metallurgy to the powertrain cores of modern machinery, cast iron has consistently proven its value—offering a rare balance of castability, strength, vibration damping, and affordability.
Technically, cast iron refers to iron-carbon alloys containing more than 2% carbon—usually between 2.5% and 4%. What sets cast iron apart is how its internal structure can be engineered through graphite shape, cooling speed, and minor alloying. This control enables engineers to fine-tune mechanical traits like hardness, strength, or thermal stability to meet demanding use cases.
Types of Cast Iron
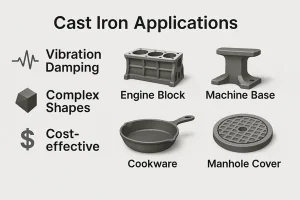
Applications of cast iron in automotive, industrial, water, and infrastructure sectors
1. Gray Cast Iron
Known for its graphite flakes, gray iron is the industry workhorse. It’s excellent for vibration damping, easy to machine, and affordable—perfect for engine blocks, brake drums, housings, and machine bases.
2. Ductile Iron (Nodular Cast Iron)
With its round graphite nodules, ductile iron offers strength and impact resistance not found in gray iron. It’s ideal for suspension parts, hydraulic valve bodies, crankshafts, and gear carriers.
3. White Cast Iron
White iron forms hard carbides instead of graphite, giving it extreme wear resistance but very little ductility. It’s common in mining, cement, and abrasive parts like liners and pump components.
4. Malleable Iron
Heat-treated white iron becomes malleable—tougher and easier to work with. While now often replaced by ductile iron, it’s still used in electrical fittings and small hardware.
5. Compacted Graphite Iron (CGI)
Somewhere between gray and ductile iron, CGI has better strength and fatigue resistance than gray iron. It’s used in high-performance diesel engine blocks and exhaust manifolds.
Comparison Table
Type | Key Traits | Common Use Cases |
---|---|---|
Gray Cast Iron | Damping, machinability | Engine blocks, housings |
Ductile Iron | Strength, ductility | Crankshafts, gear carriers |
White Cast Iron | Extreme hardness, brittle | Liners, cement plant components |
Malleable Iron | Tough, heat-treated | Electrical fittings, small parts |
CGI | Fatigue strength, mid-flex | Diesel engines, exhaust manifolds |
Mechanical Properties
- Compressive Strength: High resistance to static load—ideal for bases and frames.
- Tensile & Impact Strength: Ductile iron leads; gray and white iron lag behind.
- Hardness: White iron is extremely hard and wear-resistant.
- Vibration Damping: Gray iron excels due to graphite flake structure.
- Thermal Stability: Good conductivity and low thermal expansion help in brakes and manifolds.
- Machinability: Gray iron is easiest to cut; white iron is hardest.
Manufacturing Summary
Most cast iron parts are produced via sand casting. Alternative methods like shell molding or centrifugal casting are used for more complex geometries. Key production steps include:
- Pattern making and mold preparation
- Melting (induction or cupola furnaces)
- Pouring into molds
- Controlled cooling
- Cleaning and heat treatment
- Machining and inspection
Industry Applications
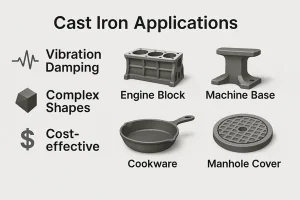
Applications of cast iron in automotive, industrial, water, and infrastructure sectors
- Automotive: Engine blocks, brake rotors, steering components
- Industrial Machinery: Gear housings, machine tool beds, compressors
- Water Systems: Ductile iron pipes and municipal fittings
- Mining & Energy: White iron used in high-wear environments
- Infrastructure: Manhole covers, bridge supports, cast bases
Advantages
✅ Casts into complex shapes
✅ Excellent vibration damping
✅ Cost-effective for large parts
✅ High wear and compressive strength
Limitations
❌ Brittle in some forms
❌ Heavy weight
❌ Difficult to weld
Design Tips
- Maintain uniform wall thickness
- Add fillets instead of sharp corners
- Use draft angles for mold release
- Include machining allowance
- Plan venting and core placement early
Standards Snapshot
- ASTM: A48 (Gray), A536 (Ductile), A532 (White), A47 (Malleable)
- EN/DIN: EN-GJL, EN-GJS
- ISO: ISO 185, ISO 1083
- China GB: GB/T 9439, 1348, 8263
Frequently Asked Questions (FAQ)
Q: Can cast iron be welded?
A: Generally no—most grades are difficult to weld due to brittleness and cracking risk.
Q: What’s the difference between ductile and gray cast iron?
A: Ductile iron has spherical graphite structures for added toughness; gray iron contains flake graphite that helps with damping.
Q: Is cast iron still used in modern industries?
A: Absolutely. Cast iron remains vital in automotive, municipal infrastructure, and heavy equipment industries.
Cast iron continues to play a vital role in manufacturing due to its excellent balance of castability, mechanical performance, and cost efficiency. With its diverse grades and applications, it remains a reliable material for engineers and product designers across many industries.
Need guidance choosing the right cast iron grade for your application? Contact us for expert support in material selection, design, and production.