Entender los defectos de fundición en la práctica de la fundición
Los defectos de fundición son fallos o irregularidades que se producen durante el proceso de fundición y que pueden comprometer la integridad estructural, la precisión dimensional o el aspecto del producto final. En los sectores que dependen de componentes de alto rendimiento -como la automoción, la construcción o la hidráulica-, entender cómo y por qué surgen estos defectos es fundamental tanto para los productores como para los compradores.
Esta guía describe los defectos de fundición más frecuentes en las piezas de fundición de hierro dúctil, hierro gris y acero. Para cada uno de ellos, cubrimos los indicadores visuales típicos, las causas subyacentes, las estrategias preventivas y los posibles remedios.
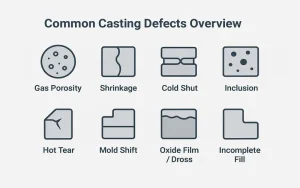
Resumen visual de ocho tipos de defectos de fundición comunes ilustrados con iconos y etiquetas.
Porosidad del gas
Apariencia típica: Pequeñas cavidades o huecos redondeados en la superficie o en el interior de la pieza fundida. Son especialmente problemáticos en componentes que retienen la presión, como carcasas de bombas o cuerpos de válvulas.
👉 Nota: Los estudios del sector indican que la porosidad del gas y la contracción representan conjuntamente hasta 50% de todos los defectos de fundición, lo que los convierte en los tipos más comunes y críticos que hay que controlar.
Causas:
La porosidad gaseosa en las fundiciones de hierro dúctil y acero suele deberse al atrapamiento de gas durante la solidificación. Esto puede deberse a:
- Humedad excesiva en el molde o en los materiales del núcleo
- Desgasificación incompleta del metal fundido
- Mala ventilación del molde o turbulencia excesiva durante el vertido
- Uso de aglutinantes con alto contenido en resina que se descomponen en gas
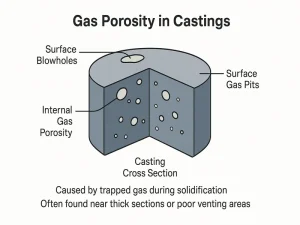
Apariencia típica de porosidad gaseosa y sopladuras superficiales en fundiciones metálicas debidas a aire o humedad atrapados.
Prevención:
- Asegurarse de que los moldes y los núcleos estén bien secos
- Utilizar materiales de carga de alta pureza y bajo contenido en hidrógeno
- Optimizar el diseño de las compuertas para minimizar las turbulencias
- Utilizar la desgasificación con argón o nitrógeno durante el tratamiento de la masa fundida
Soluciones:
- La porosidad menor puede tratarse mediante la reparación de la soldadura o la impregnación
- Para los problemas persistentes, el software de simulación puede ayudar a visualizar el flujo de gas y mejorar el diseño del molde
Cavidades de contracción
Apariencia típica: Vacíos internos o zonas hundidas que suelen localizarse en las secciones más gruesas o en zonas alejadas de la alimentación efectiva del tubo ascendente. Suelen producirse en grandes cajas de fundición dúctilo placas base de acero.
👉 Nota: Las cavidades de contracción son especialmente problemáticas en las piezas de fundición estructurales, ya que pueden dar lugar a puntos de concentración de tensiones que reducen significativamente la resistencia mecánica y la vida a fatiga.
Causas:
Las cavidades de contracción se forman durante la fase final de la solidificación, cuando el metal fundido no consigue alimentar las regiones que aún se están contrayendo. Los factores que contribuyen a ello son:
- Tubos verticales de tamaño insuficiente o mal colocados
- Falta de control direccional de la solidificación
- Congelación prematura de los cuellos de los alimentadores
- Secciones transversales gruesas con velocidades de enfriamiento desiguales
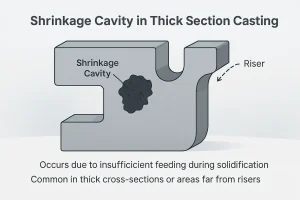
Una típica cavidad de contracción causada por la solidificación en secciones gruesas
Prevención:
- Diseño adecuado del tubo ascendente con adaptación del módulo a las zonas críticas
- Uso de escalofríos para guiar la disipación del calor
- Manguitos aislantes para ralentizar la solidificación del tubo ascendente
- Ajustar la orientación de la colada para favorecer la solidificación descendente
Soluciones:
- Modificar la geometría de la colada o aumentar el volumen del alimentador
- Reparación de cavidades mediante soldadura por arco o pulverización de metal (cuando lo permitan las especificaciones).
Cierre en frío (Misrun)
Apariencia típica: Discontinuidades finas y lineales o costuras sin fusionar en uniones en las que dos frentes metálicos no se han fusionado. Suelen verse en piezas moldeadas de pared delgadaEn las juntas horizontales o en geometrías complejas.
👉 Nota: Aunque los cierres fríos suelen ser visibles en la superficie, también pueden formar grietas internas en zonas críticas, lo que puede comprometer las superficies de estanquidad o provocar un fallo prematuro bajo presión.
Causas:
Los cierres en frío se producen cuando flujos metálicos parcialmente solidificados se encuentran pero no llegan a fusionarse debido a:
- Bajas temperaturas de vertido
- Poca fluidez de la aleación
- Vías de flujo largas o esquinas afiladas en el diseño del molde
- Elevadas pérdidas de calor a través de núcleos o enfriadores metálicos
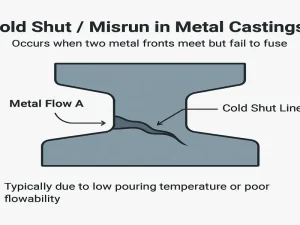
El defecto de cierre en frío se produce cuando dos frentes de metal fundido no se fusionan correctamente, dejando una línea o costura visible.
Prevención:
- Aumentar la temperatura de colada dentro de los límites específicos de la aleación
- Acortar la longitud del caudal reubicando las compuertas más cerca de las zonas críticas
- Utilizar transiciones redondeadas y filetes en el diseño de patrones
- Evitar ingestas de tamaño insuficiente que restrinjan el caudal
Soluciones:
- Modificar el sistema de compuertas para reducir la pérdida de velocidad
- Mejorar la selección de la aleación o utilizar inoculantes que mejoren el flujo
- Si la integridad estructural no está comprometida, puede ser posible una reparación localizada
Inclusiones (escoria / arena / óxidos)
Apariencia típica: Partículas oscuras o quebradizas incrustadas en la fundición, visibles en superficies mecanizadas o mediante inspección END. Pueden proceder de escoria, arena erosionada o películas de óxido.
👉 Nota: Las inclusiones se encuentran entre los defectos más difíciles de detectar a tiempo, ya que a menudo permanecen ocultas hasta que se produce el mecanizado o el fallo en servicio, especialmente en aplicaciones sensibles a la alta presión o a la fatiga.
Causas:
Las inclusiones no metálicas proceden de diversas fuentes de contaminación:
- Eliminación incompleta de la escoria durante la manipulación de la masa fundida
- Erosión de la arena de la cavidad del molde durante el llenado
- Reoxidación causada por la turbulencia del metal
- Secciones del núcleo sueltas o recubrimiento insuficiente de las paredes del molde
Prevención:
- Utilizar acondicionadores de escoria y realizar un desespumado minucioso de la cuchara.
- Introducir filtros de espuma cerámica en las ingestas
- Mantener la resistencia del molde y el acabado superficial constantes
- Reducir la altura de vertido para minimizar salpicaduras y turbulencias
Soluciones:
- Las inclusiones superficiales pueden eliminarse mediante mecanizado
- Las inclusiones profundas requieren el rechazo o la refundición, especialmente en piezas estructurales críticas.
- Las auditorías metalúrgicas pueden rastrear los tipos de inclusión hasta etapas específicas del proceso
Desgarros en caliente / Grietas térmicas
Apariencia típica: Grietas dentadas o ramificadas, que suelen producirse en esquinas afiladas, resaltes o uniones de distinto grosor de pared. Estos defectos se forman durante las fases finales de solidificación, cuando la fundición no puede absorber las tensiones térmicas internas.
Causas:
Los desgarros en caliente suelen ser el resultado de una restricción mecánica o de una mala colapsabilidad del molde. Entre los factores clave que contribuyen a ello se incluyen:
- Cambios bruscos en el grosor de la pared
- Moldes de arena rígidos con baja colapsabilidad
- Altas temperaturas de vertido que provocan amplios intervalos de solidificación
- Filetes o elementos de alivio de tensión inadecuados en el diseño
Prevención:
- Espesor de pared uniforme y transiciones geométricas suaves
- Materiales de moldeo mejorados o aditivos que aumentan la colapsabilidad
- Control de la temperatura de vertido y precalentamiento del molde
- Inclusión de muescas de alivio y núcleos flexibles
Soluciones:
- Las grietas menores pueden repararse con soldadura (si las especificaciones lo permiten)
- La corrección a largo plazo suele implicar un rediseño geométrico o materiales de moldeo alternativos
Desplazamiento del molde / Desplazamiento del núcleo
Apariencia típica: Superficies escalonadas o desalineación dimensional entre las distintas mitades de la pieza fundida, lo que da lugar a espesores de pared incoherentes u orificios desplazados.
Causas:
El desplazamiento del molde se produce por la desalineación entre la cofia y el arrastre, o por el movimiento de los núcleos internos. Esto puede ocurrir debido a:
- Fuerza de sujeción inadecuada o ajuste flojo de la cubeta
- Desgaste del patrón o pasadores dañados
- Presión metalostática elevada o sacudidas durante el vertido
Prevención:
- Refuerce las fijaciones de la mufla y garantice un registro preciso del molde
- Sustitución de los equipos de patronaje e impresiones de núcleo desgastados
- Ajuste la altura de vertido para reducir la presión del metal
Soluciones:
- El mecanizado puede ser posible si las tolerancias lo permiten
- Reconstruir o actualizar los sistemas de alineación y utillaje de patrones
Películas de óxido / Defectos de escoria
Apariencia típica: Capas finas, similares a películas, o escamas quebradizas cerca de la superficie de fundición, que a menudo sólo se descubren durante el mecanizado o en el análisis metalográfico. Estas inclusiones debilitan la resistencia a la fatiga.
Causas:
Los defectos relacionados con el óxido se forman debido a:
- Exposición del metal fundido al oxígeno durante el vertido
- Turbulencia excesiva en el sistema de compuertas
- Reoxidación causada por manipulación inadecuada de la cuchara o retraso
Prevención:
- Utilizar una atmósfera protectora (argón) o fundente para reducir la oxidación.
- Optimizar la geometría de las compuertas para permitir el flujo laminar
- Minimización de las turbulencias metálicas mediante el control de la velocidad de vertido
Soluciones:
- El óxido superficial puede eliminarse a veces mediante mecanizado
- Los óxidos internos profundos requieren refundición y revisión del gating
- Las herramientas de análisis térmico pueden ayudar a optimizar la práctica de la fusión
Relleno incompleto (insuficiencia de relleno)
Apariencia típica: Secciones que faltan, esquinas incompletas o rellenos cortos en piezas fundidas, especialmente en piezas de paredes finas o de gran superficie.
Causas:
Este defecto se debe a que el metal fundido no llena completamente la cavidad del molde antes de solidificarse. Las razones más comunes son:
- Baja temperatura de vertido o escasa fluidez
- Diseño de compuerta que restringe el flujo o induce turbulencias tempranas
- Contrapresión de gas por mala ventilación
- Características del molde demasiado complejas
Prevención:
- Aumentar la temperatura de vertido dentro de los límites de la aleación
- Mejorar la relación de inyección y el escape de aire de la cavidad del molde
- Simplifique la geometría de las piezas de fundición o divídalas en diseños de varias piezas
- Aplicar técnicas de vacío asistido cuando proceda
Soluciones:
- Evaluar las simulaciones de relleno para localizar las zonas problemáticas.
- Refundición con sistemas de flujo y ventilación corregidos
Métodos de ensayo no destructivos para defectos de fundición
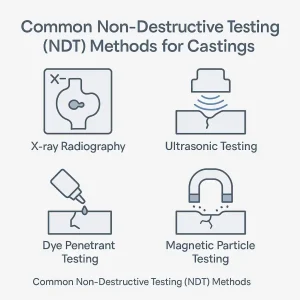
Métodos END comunes utilizados para la inspección de piezas de fundición: Rayos X, ultrasonidos, líquidos penetrantes y partículas magnéticas.
Método de ensayo | Defectos detectables | Materiales adecuados / Usos | Notas |
---|---|---|---|
Radiografía | Contracción interna, porosidad, vacíos | Piezas de fundición complejas, piezas de pared gruesa | Excelente detalle; más caro |
Pruebas ultrasónicas | Grietas subterráneas, inclusiones | Grandes secciones, acero/hierro dúctil | Requiere habilidad del operario y una buena superficie |
Pruebas con líquidos penetrantes | Grietas superficiales, cierres fríos | Metales no porosos (aluminio, acero) | Sencillo, asequible; sólo visible en la superficie |
Partícula magnética | Defectos superficiales y cercanos a la superficie | Metales ferrosos (hierro fundido, acero) | Rápido y fiable; limitado a piezas magnéticas |
Estos métodos de ensayo ayudan a identificar defectos internos o externos antes del mecanizado o la entrega, garantizando que sus componentes de fundición cumplen las especificaciones dimensionales y de rendimiento.
Reflexiones finales
Los defectos de fundición pueden afectar significativamente al rendimiento, el coste y la satisfacción del cliente. Con una comprensión clara de las causas de cada defecto y de las estrategias correctivas, tanto las fundiciones como los compradores pueden adoptar un papel proactivo en el aseguramiento de la calidad.
¿Busca asistencia técnica o análisis de defectos? Contacte con nuestro equipo para obtener asesoramiento experto y soluciones de fundición personalizadas.